Rapid Axis for Sheet Metal Prototyping
Rapid Axis provides competitively priced, quality parts; quickly. With short lead times and a superior focus on quality and customer service, Rapid Axis is the easy choice for Sheet Metal Prototyping services. We have cutting, bending, forming, welding and finishing capabilities that can get you your bracket, fixture, enclosure or any part you are working on in budget, in spec and on-time.

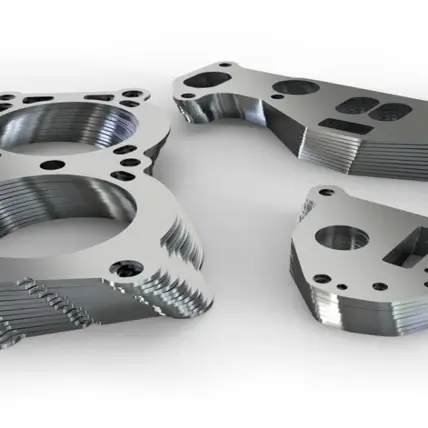
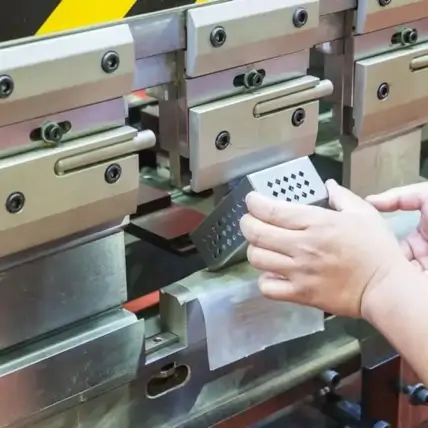
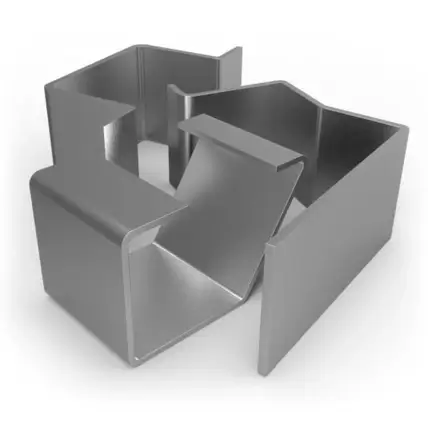
Why Rapid Axis is the best choice for Sheet Metal Prototyping
With consistent reliable quality, excellent pricing and best in industry customer service Rapid Axis is the clear choice for your next Sheet Metal component or assembly. We offer free 1st Level Inspection on all projects and quotes to match print without blanket statements about loosened tolerances. With no qty minimum and quick lead times, our sheet metal prototypes can rapidly take you from prototyping to production for any Sheet Metal project. Our best in industry customer service and competitive pricing will keep you coming back for everything from a simple laser cut plate or a fully formed, welded, finished and hardware assembled housing.
Cutting, bending, forming and welding are supported
Parts made to match customer drawings
Finishing and hardware installation supported
Technical
General Tolerances: Flat parts +/-.010” or better feature to feature for parts with forming or bending +/-.030” or better feature to feature. Rapid Axis quotes to meet drawing tolerances
Cutting Size: 10’ x 20’
Bending Size: 12’ Press Brake
Hole Punch: 3” or Larger
Welding: Spot welding, continuous welding, laser welding and more
Finishing: Bead Blast, Powder Coat, Anodize, Paint, Pad Print, Chem Film, Gold Plating, Silver Plating and more
See Finishes page
2nd Operations: Hardware Installation, Assembly, Post Machining
Materials: Aluminum, Bronze, Copper, Stainless Steel, Steel
See Materials page
What is Sheet Metal Prototyping?
Sheet metal prototyping is a form of sheet metal fabrication, which is in turn a part of sheet metal machining. For reference, sheet metal refers to any piece of metal that’s typically under 1/4” thick. Thinner materials allow for easier forming and workability to obtain your desired net shape.
Sheet Metal fabrication methods include bending, forming, welding, hardware installation, powder coating, painting, drilling, cutting, milling, installation of hardware and other types of finishing. A sheet metal prototype is made using one or more of these methods in order to verify the form and function of the part before production.
Typically the initial manufacturing operation of sheet metal forming starts with cutting a blank with a laser cutter or waterjet before forming, welding, hardware installation and finishing.
Some standard machining practices and equipment are used as part of the sheet metal fabrication process, though sheet metal does have specialized tooling and processes associated with it.
Sheet Metal Prototyping Applications
We understand that sheet metal prototype fabrication is a little tricky to understand. To better explain things, let’s explain some major applications and benefits of using sheet metal for prototype fabrication. This will compare directly to other prototype manufacturing methods.
It’s Easy to Process
One of the biggest selling points of sheet metal fabrication is how easy it is to cut and form Sheet Metal. There are many more design constraints associated with making sheet metal parts, but the fabrication itself is easier, quicker, cheaper and more repeatable with quicker price breaks for high quantities.
With thicker materials, more time is required for every operation. Drilling a series of thru-holes could take four times longer if it’s done on a plate as compared to sheet metal.
In addition, the material is a lot easier to handle, store, and move around. This is because sheet metal is so thin.
As long as a fabricator has experience working with sheet metal, they can attest to how much easier it is to work with — as long as the design is correct.
Since it’s easier to fabricate, you’ll enjoy lower quotes and faster turnaround times and very quick price breaks on higher quantity orders.
Make Multiple Parts from One Stock Sheet
Another perk of using sheet metal is that the raw material typically comes in large sheets. It’s common to buy commercial sheet plates that are 6’ wide and 10’ long.
A single piece of sheet metal can be used to make dozens of prototype iterations for your project. It all depends on how we can rough cut it and utilize the square footage of the sheet.
Luckily, this means that sheet metal fabrication shops can save money on raw material costs. Instead of buying ten small sheets of metal, we can buy a single massive sheet and save on shipping and purchase costs. These savings go directly to our customers.
You Can Bend or Form Assemblies
With sheet metal, you can bend and form multiple walls, recessed features and flanges onto a single part. This allows you to avoid welding and tapping holes when you want to make an assembly. Instead, you can have a single, solid piece of sheet metal that’s bent to a shape that suits your design.
This saves processing time as well as design time. In addition, it makes maintaining the part much easier in the future. You don’t have to inspect torqued bolts, check weld seams, or replace multiple parts. Instead, you just have one product to worry about.
Hardware Can Easily Be Used
Sheet metal has a special series of fasteners that are self-clinching, broaching, flaring, surface mounted, or welded. There are hardware fasteners that exist for almost any application and they are readily available and easy to install.
This isn’t always possible with thicker materials or other fabrication processes. Using off the shelf fasteners such as PEMs, Cable Tie Mounts or Studs and Pins can save a lot of time when it comes to fabrication and assembly. It also makes it easier to field-fit parts without going through a thorough design process.
Create Lightweight Parts
Another benefit of sheet metal is that it’s inherently a lot lighter. Plates start getting exponentially heavier as you pick thicker options.
With sheet metal, it’s simply to make a part that can be easily carried around by hand. Even a dense stainless steel sheet metal part is light enough to move it alone.
If you have an application where you need some level of non-load-bearing protection and you want to keep the weight down, sheet metal fabrication is going to be your best bet. Other methods of lowering the weight involve choosing more expensive materials or compromising the mechanical integrity by drilling holes in a part.
By choosing sheet metal instead, you don’t have to alter your design or go over budget for a single part.