Rapid Axis for SLS Printing
Rapid Axis provides competitively priced, quality parts; quickly. With large format EOS and Sinterstation machines at our disposal, Rapid Axis is well suited for prototype and production SLS projects alike. Rapid Axis keeps most commonly processed materials available on demand such GF Nylon, Nylon 11 and CF Nylon.
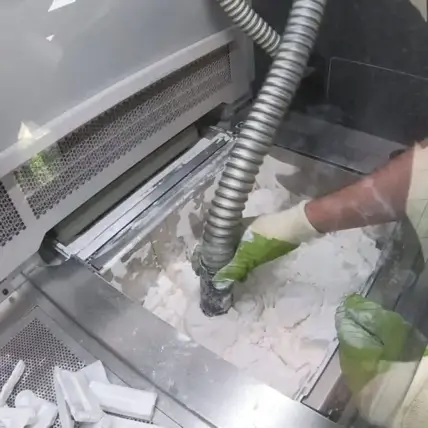
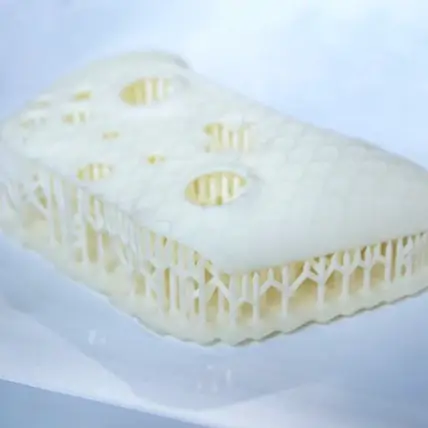
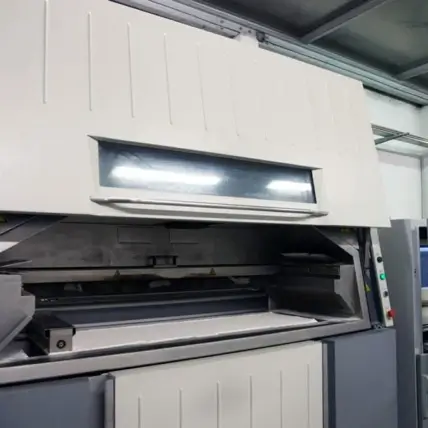
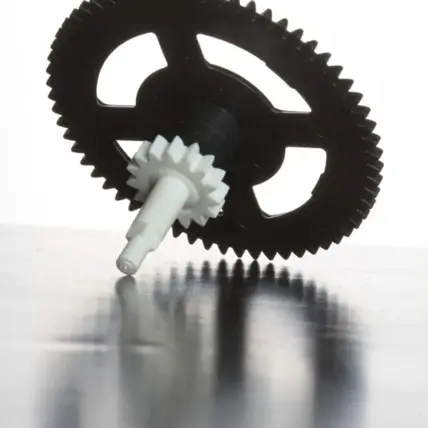
Why Rapid Axis is the best choice for SLS
Experience. Rapid Axis is the choice for prototyping and production for multiple aerospace and medical device customers. We’ve fabricated components of all shapes and sizes with various hardware and finishing requirements and we’ve delivered them all in spec and on-time. If you are looking for a subject matter expert in SLS to partner with you on your next project. Look no further, Rapid Axis is the best choice in SLS fabrication.
Prototyping or production
Finishing supported
Best in industry customer support
Technical
General Tolerances: +/- 0.010” for the first inch, plus +/- 0.002” for every inch thereafter or better
Layer Thickness: .0045”
Build Size: 26″ x 15″ x 23″
Cosmetics: Dyeing, Painting, Plating
2nd Operations: Post op machining, hardware installation, split and bond
Equipment: 3D Systems, EOS
Materials: PA12, PA603 CF, PA606 FR, PA615 GS, PA2200 Ultra White, PA850 Black
See Materials page
What is SLS Printing?
SLS printing is a form of additive manufacturing. It stands for Selective Laser Sintering, and that gives a hint as to how the technology works. A build chamber is filled with a layer of nylon-based powder. From there, a laser shines against a mirror and into this chamber.
The laser is stationary, while the mirror makes slight adjustments. As a result, the laser’s beam in the build chamber moves around.
In the build chamber, the energized laser heats up and sinters the nylon powder wherever the laser traces. After a few seconds, the sintered powder cools enough into solid nylon along the line. The laser will be used to trace a single layer of the part, then another layer of powder is laid down and the process is continued.
After enough layers and time, the finished 3D part is created in the build chamber. It goes through brushing then treatment, then it’s ready for any finishing steps and shipment to our customer.
This sounds like MJF, another form of 3D printing that uses nylon as the print material. The key difference is that SLS printers sinter the powder together which is less expensive, creates lighter products, and doesn’t have the same issues with printing larger, solid parts.
In terms of fabrication, SLS and MJF are probably the closest options if you want a direct comparison. If you want to step outside of 3D printing, then you would consider injection molding or CNC machining if you want a comparable part.
SLS Printing Applications
In terms of high-quality plastic parts at affordable pricing and fast turnarounds, SLS printing is a great option. If you want to use this method for your next project, consider the following advantages and applications.
Great for Small-Batch Orders
Across the board, 3D printing is typically the best option for small-batch orders. When it comes to SLS, this still holds true. If you compare SLS printing to CNC machining or injection molding — the two other options — neither can compare for small-batch orders.
Injection molding a small order will cost way too much money and the lead time could be multiple weeks or months. CNC machining would offer a more favorable lead time, but the price would still be too high.
SLS printing hits the sweet spot of affordability, quality, and fast turnaround times. Whenever a customer approaches us for advice on small-batch plastic units, we almost always point them towards 3D printing.
Cost-Effective Per-Unit Option
It’s worth highlighting the cost-effective nature of 3D printing. With SLS printing, the per-unit cost is essentially the same, regardless of how many units you order. This makes prototyping a handful of units very affordable.
With CNC machining, a lot of time is spent upfront creating a program for the part. If you’re just looking for a few units, you won’t see any cost savings. Injection molding typically requires orders in the thousands of units before the per-unit cost starts to even out — there’s a large upfront cost to make the mold and tooling.
SLS printing is almost always the least expensive option for orders in the single digits, and it’s competitive as order volumes get into the double digits. Above that, you should consider other manufacturing options.
Design Freedom
Compared to other 3D Printing processes SLS boasts a major advantage. The components do not require support as they are suspended in a powder cake during the fabrication process. Components are then broken out of this cake and cleaned off without the need to remove supports. The only caveat is that there has to be a way to remove powder, this could be just a simple hole. As a result this makes SLS a great choice for ducts, tanks (gas, oil) or object with organic geometry.
Wider Material Options
In addition, there are more material options as you look at SLS printing. We offer six different nylon-based materials. Some of our materials are filled with additives like carbon or glass in order to fine-tune the material properties.
We also have heat-resistant nylon that’s better in heated applications.
Keep in mind, SLS printers deal specifically with nylon-based materials. You won’t be able to print any hard plastics or metals, but that typically isn’t an issue since nylon is such a versatile option.
It’s Easy to Post Process
Sometimes, finishing steps are essential for a part. If you need a part painted, dyed, or sanded to a fine surface, your options are limited. With SLS printers, this is possible. It has to do with the layer properties.
Since a laser is used to sinter the nylon material together, the final product is more robust and able to be processed. This allows us to paint them and sand the product down to a showroom-ready level of detail.
With the ability to paint units, SLS parts become more desirable. You can use different colors to visually differentiate different iterations, product lines, and versions of a part. It also helps highlight parts that need to be noticed for safety reasons.