Rapid Axis for CNC Laser Cutting Services
Rapid Axis provides competitively priced, quality parts; quickly. With unique equipment formats and types Rapid Axis has capability of cutting both thin and thick materials via Laser Cutting. Whether you have a one off prototype or a flat pattern for a production run, Rapid Axis can help. If your flat pattern requires forming operations, hardware installation or finishing Rapid Axis has the capability to support it all.
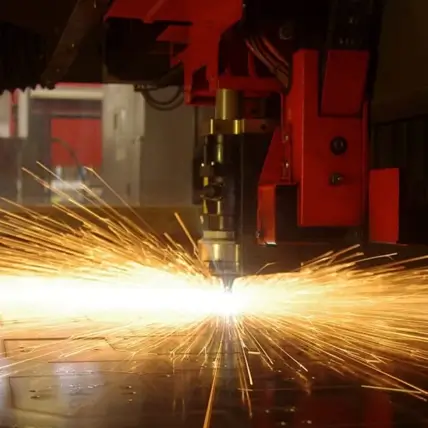
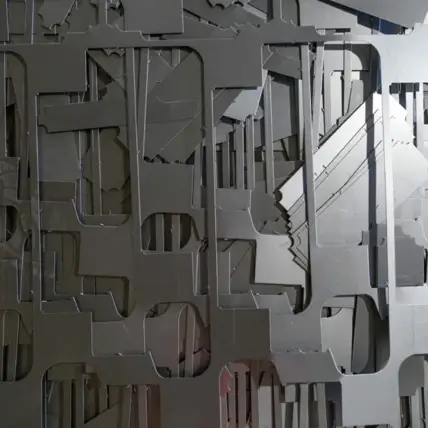
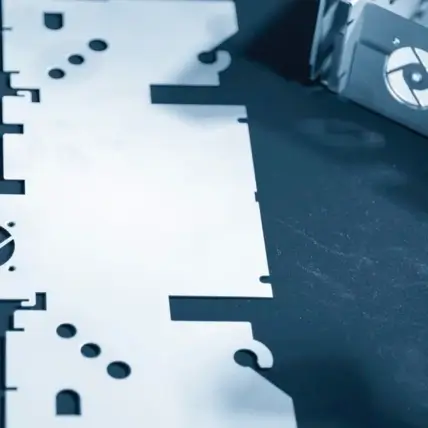
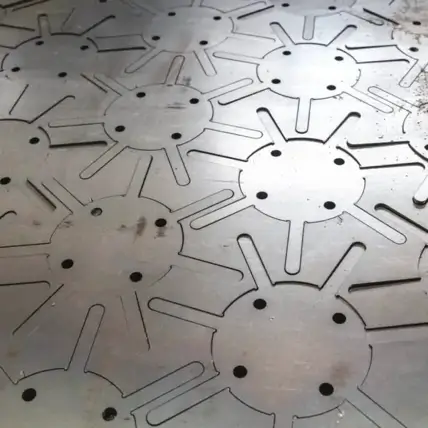
Why Rapid Axis is the best choice for CNC Laser Cutting
With quick lead times and attention to part quality and tolerances Rapid Axis is the clear choice for CNC Laser Cutting services. We’ll quote your components quickly, competitively and in spec and provide post order support as well. Rapid Axis can support many custom material requirements for precision laser cutting as well as second operations and inspection levels. See why Rapid Axis is known for best in industry customer service and try us out for your next Laser Cutting project.
Quick lead times
Excellent customer support
Vast material selection
Technical
General Tolerances: +/-.010” or better is typical and dependent upon material
Thickness: Laser cutting can process materials up to 0.75” thick
Table Size: 120” x 60”
Finishing and 2nd Operations: Anodize, PAA + BR127, Powder Coat, Paint, Chem Film, Alodine, Chromate, Heat Treating, Black Oxide, Zinc Plating, Polishing, Bead Blast, Electropolish, Gold Plating, Silver Plating. Brushing, Vapor Polish, Teflon Impregnation, Park Marking, Logo Work, Hardware Installation, Assembly and more
See Finishing page
Materials: ABS, Acrylic, Aluminum, Copper, Bronze, Brass, Delrin, HDPE, Nylon, Polycarbonate, PEEK, Polypropylene, PTFE, Stainless Steel, Steel Alloys, Titanium, UHMW PE, PVC, Thermal Pad, Transfer Tape, Adhesive Sheets and more
See Materials page
What is Laser Cutting?
Laser cutting is an interesting style of manufacturing typically used on materials that come in “sheet” thicknesses. It uses a high-powered laser to physically cut through sheet materials. The concentrated beam generates a lot of power and heat, which is used to slice through a variety of materials such as double sided tapes, plastics and metals.
The laser is affixed to the head of a CNC gantry. Typically, the gantry has 3 axes of motion. It can move in the x, y, and z directions. The sheet sits flat on the table of the laser cutter, and the head moves around to make the shape.
The operation itself is very fast. This setting can be fine-tuned and varies from machine to machine. At Rapid Axis, we program our laser cutters to prioritize quality with speed being the second priority. This results in smoother cuts and still yields very fast turnaround times for laser cut parts.
Laser cutters work by uploading a 2D flat pattern of the part you want to make. There is a program in the CNC laser cutter that determines the path, speed, z distance, and different parameters. After hitting the “go” button, the laser cutter will go through the operation without pausing.
A laser cutter isn’t restricted to just cutting outlines of parts. It can also create internal holes of various different geometries. The key is that it has to cut the internal features before cutting the outside shape. This gives designers a lot of freedom.
Laser Cutting Applications
Let’s review some of the benefits of laser cutters. There are plenty of applications that we’ve used laser cutters on in the past few years. Maybe this technology is perfect for your upcoming design.
Very Fast Operation
A CNC laser cutting machine is much faster than any CNC mill we have on our floor. It’s largely due to the power of the laser. In reality, the laser’s movement is limited to upkeep reliability and quality, it’s not limited to how quickly a laser can cut through sheets of material.
Compared to traditional machining, laser cutters win by a mile. Since they’re so much faster, you can enjoy shorter turnaround times for any sheet metal or plastic component that we laser cut.
Make Multiple Pieces with One Sheet
Whenever we use the laser cutter, we try to optimize the material that we use. Our operator will set up the program to fit as many parts onto one sheet of material before firing up the laser cutter.
By doing this, we’re saving time and money on each project. You can get a dozen units made from a single sheet of material and a single program on a CNC laser cutting machine. This saves a lot of time and money for us and you.
Loading sheets and programming the laser takes a little bit of time before each cut. Doing it too much will slow down the process and take up too much material.
Requires Very Little Startup Effort
Once a laser cutter is turned on and running, starting a project takes very little effort. As we mentioned, all it entails is loading material onto the table and setting up the program. If it’s a repeat order, the program has already been made. That means we just have to hit a single button after loading the material, then the machine starts.
All laser cutters are fully calibrated and set up to run. By keeping the machines in this state, we don’t have to waste time before each cutting project. It also ensures you get tight tolerances, high repeatability, and fast throughput for each project you order through Rapid Axis.
Can Cut Various Thicknesses
Laser cutters aren’t only made for a single thickness of sheet. Since there are dozens of different thicknesses to choose from, this is good news.
Laser cutters come with a thickness range that they can work through. Ours can cut materials up to 150mm or 5.9” dependent on alloy type though at higher thicknesses other methods are typically more suitable. All we have to do is measure the sheet before firing up the program. By inputting the thickness into the computer, the laser will adjust the speed and power of the plasma.
Can Skip the Line at the CNC Milling Machine
During busy seasons, our CNC milling machines can generate a queue. Instead of waiting for other projects to finish up, you can skip the line and go straight to our laser cutter. Since the operational speed is so fast, the wait time is much lower.
In a busy shop, the turnaround time could be determined by the queue. By skipping the line, you’re expediting the project and getting your parts back much quicker.
Allows a Lot of Design Freedom
Laser cutting technology allows your designers to have a lot of freedom on the drafting table. It’s also a lot easier to design since you only have to look at the top view of the part.
There are some structural limitations to think through, but laser cutters can pretty much cut anything you can draw on your CAD screen. It also allows for tight tolerances to be upheld without the need for secondary steps to make the features.