Intro
Die casting is a great way to get a number of nearly identical parts made out of metal. The process is faster than most traditional machining options, and the final part is typically less expensive. The biggest driving decision in die casting is the material choice.
There are a few different aluminum alloys that can be used in die casting, depending on the shop. In this quick guide, we’ll explain six of the most popular options, explain their pros and cons, and help you pick the right option for your project.
Why the Alloy Matters
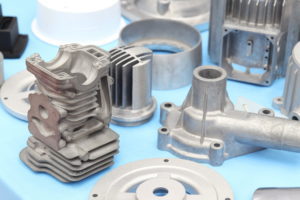
An alloy, by definition, is the combination of two or more materials to make a single compound. In this case, it’s the process of mixing aluminum with other elements.
Alloys will also mix together different material properties of the materials that go into the mixture. With different levels of copper, zinc, and chromium, you can completely change how the final part acts and performs.
In our experience, there are a lot of instances where one alloy will work perfectly, and another alloy will fail catastrophically. A good example of this is strength requirements or a material’s resistance to corrosion.
If there’s not enough aluminum in the mixture, then the part won’t be as strong. It’s possible that a low-aluminum content alloy will fail and collapse in the same application where a high-aluminum content alloy will have no problem.
A380 Aluminum Alloy
Going with A380 is a great way to save money and lower the overall weight of your part. It’s more of a “general-use” option that doesn’t offer the same ruggedness or corrosion resistance that other alloys have, but it’s less expensive and easier to work with.
Even if you have an intricate part with tough geometries, there’s a good chance that A380 will work during the die-casting process.
In our shop, A380 is the most popular option, and it’s typically what we recommend to customers who don’t have specific requirements for their parts.
Despite the lower price tag, this alloy is still very strong, has impressive electrical conductivity, and can resist heat well.
A383 Aluminum Alloy
With A383 aluminum alloys, you get a lot of the same features that A380 has. The difference is that A383 is even better at filling molds, so we might suggest this material option if your part is exceptionally intricate.
A383 performs better under heat and poses a lower risk of cracking than A380. It’s also a little more expensive, and not as durable — but it offers even better strength at high temperatures.
A360 Aluminum Alloy
A360 aluminum alloys are the strongest option so far on this list. They have great strength, especially at higher temperatures, an impressive ductility, and very good corrosion resistance.
The downside is that this alloy is a little tougher to cast. To be more specific, we noticed that it has trouble filling molds with a lot of tight corners and internal cutouts or features.
If you have a simpler part that requires higher strength and you don’t mind paying more per unit, then A360 might be the best option for you.
ZA-8 Aluminum Alloy
The first option we’ll mention in the ZA-series (or zinc aluminum alloys) is the ZA-8 aluminum alloy. This option has a low level of aluminum which translates to a higher density and lower melting point.
As far as ZA-alloys go, this is the only option that can be used in a hot chamber. It also means that the finished part will have a much higher overall strength and durability.
ZA-12 Aluminum Alloy
By adding more aluminum to the mixture, you get a ZA-12 aluminum alloy. It has less aluminum than ZA-27, the next option on this list. As you might expect, it offers material properties somewhere between both options.
It has to be used in a cold chamber for casting, but it has a great combination of strength and castability. In other words, we can still work with this alloy without big problems, and you get a part that meets all of your strength requirements.
ZA-27 Aluminum Alloy
As we mentioned ZA-27 has the highest amount of aluminum in the ZA-series that is used for die casting. Of the three, it’s the most difficult to cast, so it can only be used for certain projects.
The tradeoff is that ZA-27 is incredibly strong. It has the highest strength, lowest density, and highest melting point.
Of course, it can only be used in a cold chamber and requires extra thought into the cooling rates. If you find a shop that can use ZA-27 in die casting, then you’ll have access to the strongest aluminum-based material.
Conclusion
Now you have a better understanding of which aluminum alloys to choose between for your next project. We understand that this is just a brief introduction to these aluminum alloys, and we urge you to reach out to our experts at Rapid Axis to learn more.
Our shop is capable of running full die-casting operations for your project. We’ll help you through the process from suggesting design decisions to making final production units. Get a free quote today.