Aerospace and Defense
Our History with Aerospace & Defense Companies
Throughout our years in business, we’ve worked with companies such as NASA and Collins to provide only the best custom components. Our collaboration and machining expertise always left them with a good experience.
We offer CNC machining, Sheet Metal, industrial-grade 3D printing, and a wide range of finishing processes. Our team can handle sheet metal or stock plate fabrication, so you don’t need to change your design for our accommodation.
We execute projects from the gen 0 prototype to the final, installed part. Along the way, we can provide tips and expertise from a machinist’s perspective to enhance your design.
Rapid Axis is familiar with and enforces EAR/ITAR compliance internally and can work on defense related projects or items with ECCN restrictions in a safe and compliant manner. Contact us for file sharing instructions if your project falls into the above category.
Why Aerospace & Defense Companies Choose Rapid Axis
We’ve worked with a number of aerospace and defense companies in the past. They choose our professional team at Rapid Axis for a number of different reasons.
High-Strength Material Options
In certain applications, the strength of the material can make or break your project. Whatever high-stress, high-temperature, high-impact part you need made, we can handle it. We have access to material vendors across the globe, and we can handle a wide range of different materials.
We stock 7000-series aluminums and different titanium alloys. On top of that, we have experience machining these materials, so we can achieve the best results.
Fast Turnaround Times
Another thing that we’ve learned with these projects is that timelines can be very aggressive. If you trust a shop that can’t handle fast turnaround times, you’ll be blamed for the shop’s shortcomings.
At Rapid Axis, our focus is to get you the highest-quality product in the shortest time. That means that you won’t need to stress about timelines, and you’ll get your parts back sooner.
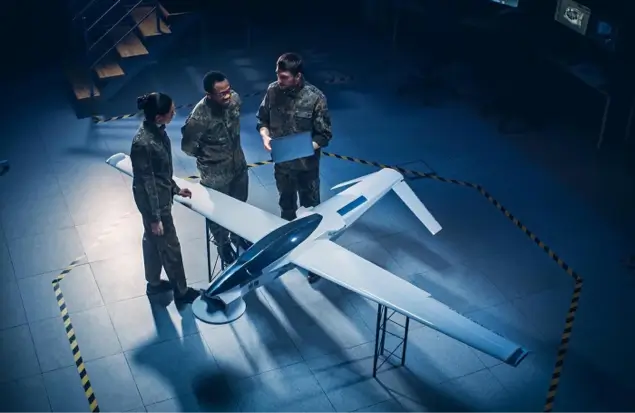
Fully Customized Parts
In our experience, there are very few “cookie cutter” solutions in the aerospace and defense world. Almost every project that we’ve seen has been a fully customized part that solved a unique problem.
The good news is that Rapid Axis isn’t a “cookie cutter” machine shop. We’ve been creating unique, high-precision parts for decades. We always appreciate an opportunity to make a customized part from scratch. All you need to do is provide the 3D model and drawing, and we’ll handle the rest.
Full Inspection with Documentation
Depending on your organization, you might have some strict inspection requirements that need to be met before you can accept a part. At Rapid Axis, we perform on-machine inspection and fill out the documentation to your specifications.
We don’t want a lack of a paper trail hurting you in the long run, especially if your company requires it. By providing inspection reports, you’ll know that all of our parts were made to the right specifications and you can prove it to your leadership.
Robust Finishing Capabilities
Something that sets us apart from other shops is our ability to offer a number of different finishing steps. We understand that your industry has some unique specifications when it comes to surface finish and coatings.
To make things easier, we offer anodization (including PAA + BR127), powder coating, heat treatment, and electroplating through a curated network of partners. By being able to offer all these finishing capabilities with quality guaranteed; Rapid Axis makes your project easy to manage with one point of contact.
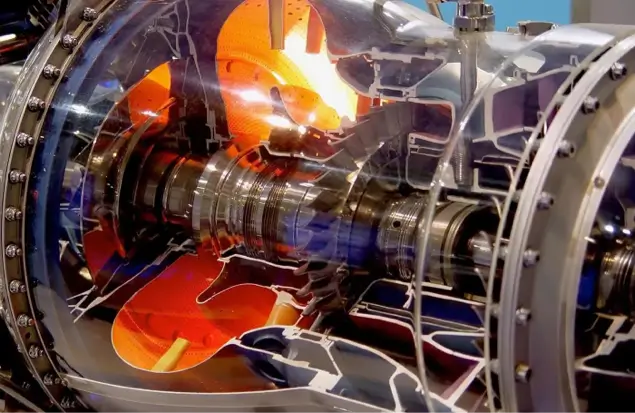
A Partnership from Prototype to Production
We had an ongoing project with a large defense contractor, and their project manager pointed out how useful our partnership was throughout the project. In that specific case, we started out by prototyping their part and ultimately created 100 production-grade units for them.
We understand that there can be a lot of secrecy and trust in these industries. By sticking with one vendor throughout the project’s lifecycle, you can minimize your risks. It also helps your timeline and budget by sticking with a shop that can execute every stage of the project.
Low-Volume Manufacturing
Most aerospace and defense companies are looking for low-volume manufacturing. These aren’t applications where you need to make a million products for an open market.
Luckily, we have extensive experience working on lower-volume projects. Namely, we can handle CNC machining and DMLS 3D printing. This will help you get your parts at affordable prices, high qualities, and fast turnaround times.
When we get started together, we’ll learn more about the application for your part. From there, we’ll use the best available machining methods.
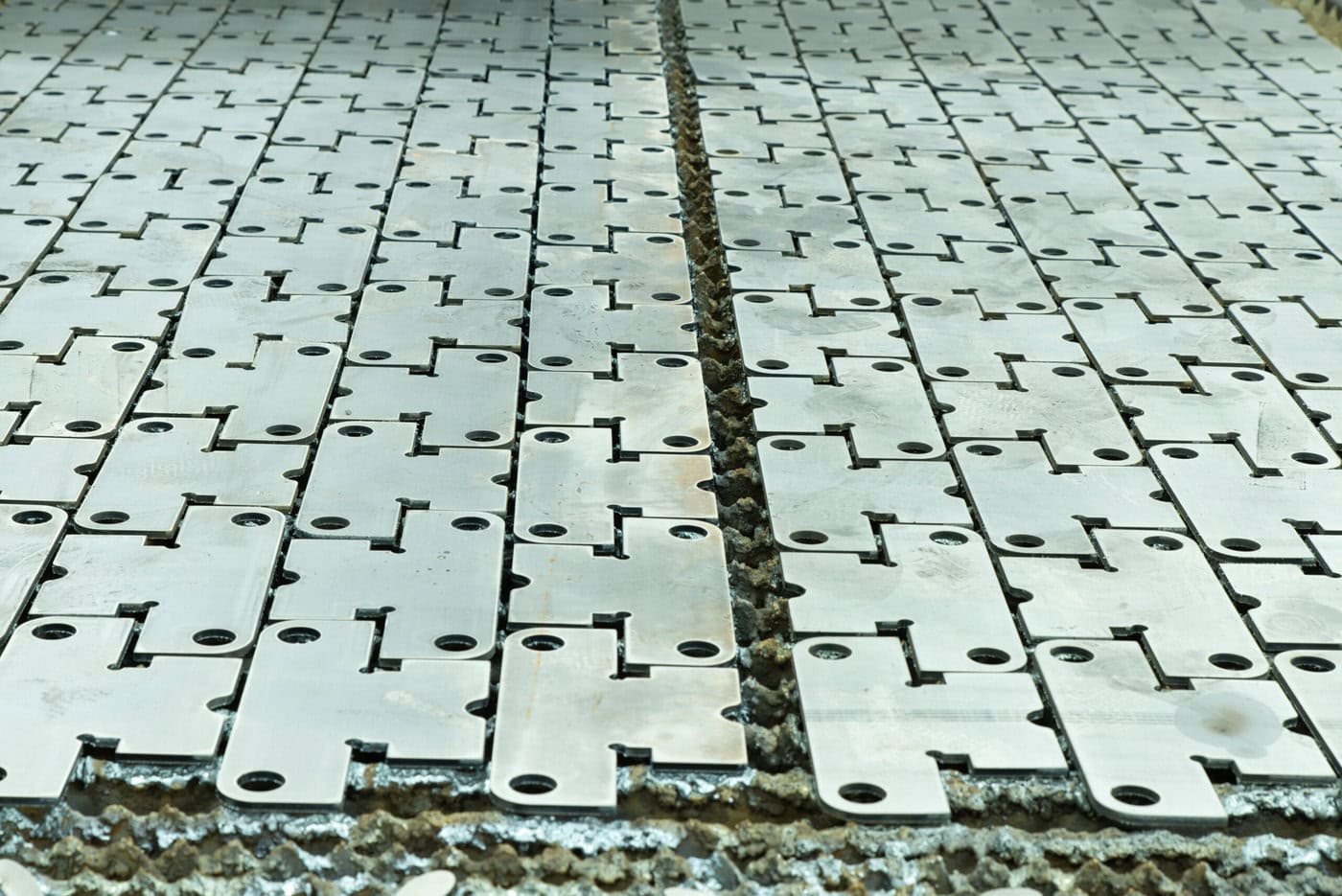
Bulk Parts When Needed
In other cases, you might need a large quantity of metal or plastic parts. That’s another option that we offer at Rapid Axis. We can handle injection molding, die casting, and urethane casting. These options will help you get products in large quantities.
This can be anything from a rubber knob to a plastic button. Regardless of the application, we can handle it and send out units in the thousands to your loading dock.