By Ben Carlson
Cooperative product manufacturing in the electric vehicle space is set to dominate global markets in 2020, with an increase in production across all major producers. Rapid Axis is a prototyping specialty manufacturer in Redwood City, California and supports multiple EV companies’ prototyping and production requirements. Industry-wide, machining of vehicle components has begun a dramatic shift away from complex machined moving parts and toward a more static suite of components. Electric vehicles, by design, rely less on heavily machined and variable parts and are more aligned with highly engineered parts that are interchangeable between models. According to Allied Market Research, the electric vehicle market will tip over the $500 billion mark in the next five years.
Source:
https://www.alliedmarketresearch.com/electric-vehicle-market
With a changing political climate, automobile manufacturers are under pressure to provide more fuel-efficient means of transportation in both commercial and consumer markets, as well as drive manufacturing costs of supporting technologies along to Tier 1, 2, and 3 providers as well as OEM production. Segmental production of prototyping has had a profound effect on US manufacturing.
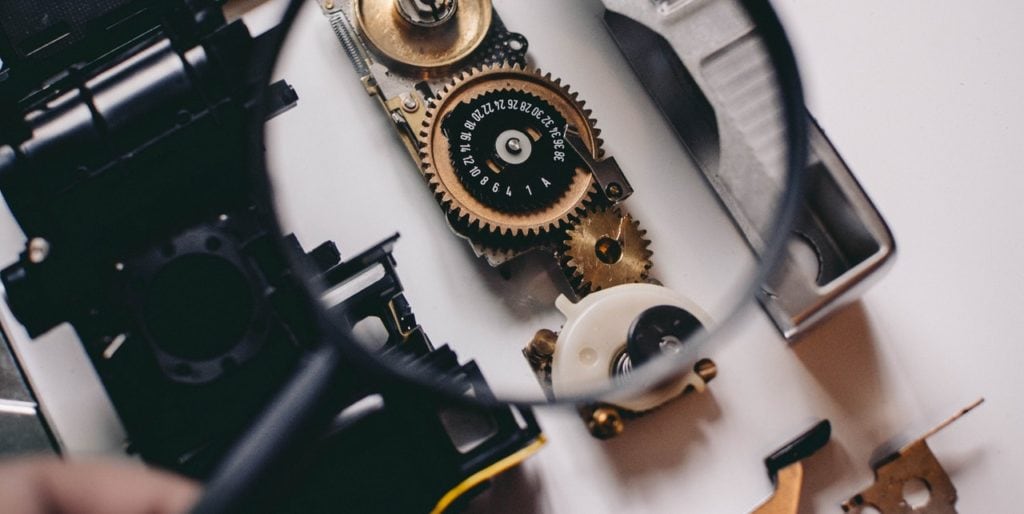
Current market strength is showing favorably toward hybrid electric vehicles (HEV) leading the sector, followed by plug-in hybrid electric vehicles (PHEV), and battery electric vehicles (BEV). Expanding business operations and tooling purchases in the US sector have driven competitive manufacturing growth of EV products across component suites in these vehicles.
Rapid Axis has been at the forefront of developing technologies in the electric vehicle market, particularly with electronics enclosures. Unlike combustion engines, the electric vehicle market lists toward durable and rated enclosures for sensitive electronics. International certifications for these new enclosures are measured on the Ingress Protection rating at a standard above or beyond what might be typically seen in modern vehicles, which reduces intrusion from dust, water, and road particulates that may have an impact on vehicle life and functionality. With no moving parts in a battery for BEV cars, a minimum rating of IP 66 has been adopted across the industry. These rated enclosures are utilized in not only batteries but high voltage areas of the vehicle as well. By limiting and redirecting current through microprocessors, these vehicles are well-suited to provide efficient means of transference of power throughout the system from contactors to potentiometers.
Interior component machining and printing allow for rapid iteration during the development phase of component production. ECU body control electronic modules are among the several parts used in these systems, along with thermal and power controllers. MCU or media control unit parts are rapidly changing with new models and are available for production through OEM clients as well as aftermarket suppliers. PCBA internal board housings are adapted regularly for changing models and design needs.
As the US rolls out more charging stations, clients across the industry are turning toward branded suites of power supply, thus leveraging market growth and recognition. Internal to the vehicles, charging port electronic controllers are precision engineered and developed by Rapid Axis. Precision engineering and development allows manufacturers and energy suppliers to level loads supplied to vehicles for both standard and rapid charges as consumers are provided with more options to travel further distances. Infrastructure growth and adoption of electric vehicles are slated to increase demand for production capabilities of manufacturing through companies like Rapid Axis.
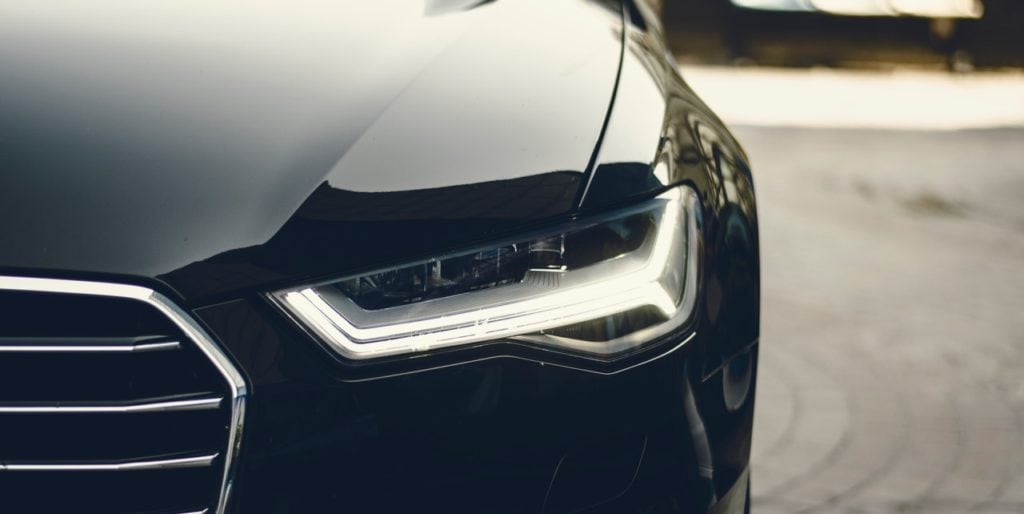
Drive train components of electric vehicles rely heavily on the balance of weight distribution and structural integrity, as well as maintaining more significant corrosion and leak resistance for parts. The drive train of today’s modern electric vehicle provides the central computer with thousands of data points each second. Every piece of the system is continuously monitored and updated to allow for efficient control from the driver’s seat as well as maximize electrical utilization through components such as a chassis yaw rate sensor control module, which seeks to improve overall handling and adjust power to each wheel. Rapid Axis serves clients in component manufacturing and testing through offering a robust suite of prototype and production capabilities.
Applications of prototyping in electric vehicles remain a robust and growing market, showing no signs of slowing. Low volume 3D printed parts allow manufacturers to inexpensively test real-world applications of new designs, allowing for the rapid transformation of delivery systems embedded in these machines. Additive manufacturing continues to lead teams to recognize the benefits of developing with prototyping operations. By utilizing rapid prototyping in the design phase, lead times for development can be shrunk from cost-prohibitive tooling with more traditional manufacturing methods. By developing integrated parts for EV components digitally and then producing with Rapid Axis, lead times can be as short as days as opposed to weeks or months with traditional machining operations.
Analogous materials to real-world applications are utilized in 3D printing systems available to modern manufacturers. The thermoplastic application of Nylon 12 in an SLS component, for instance, is durable, machinable, and able to withstand temperature fluctuations not previously available in recent years. In addition to thermoplastic components, additional low tolerance printed alloy materials are available to produce detailed housings and other complex assemblies used in electric vehicle construction with tolerances to the thousandth with ever-increasing clarity. Nearly all iterations of design can be sourced through printing and machining services at Rapid Axis that are capable of producing products in almost any size. Post-processing of additive prototypes and production runs is available to provide turn-key solutions to any manufacturing need and volume by working closely with design teams for enclosures and components to deliver fully functional finished goods ready for beta or production runs.
With lead times for additive manufacturing steadily declining and resolution and material science keeping up with the demands of electric vehicle companies, the machine shop of today is better suited to handle the most complex and imaginative engineering possible. Balancing material properties and engineering requirements is a specialized task when developing new products. For material selection and resolution to be highest, products such as fusion deposition modeling, FDM, offer tolerances of the highest fidelity and environmental resistance. One such application of FDM parts include the powder-based PEKK additive process wherein high performance, and dimensionally stable components can be produced. Additive manufacturing using the FDM process can utilize a vast array of materials to be used in structural applications as well as insulating piezoelectric parts or components used for tooling where fire retardancy is of crucial concern. Antero PEKK parts are consistently mechanically stable and lighter than other materials while allowing their application in lubricated or acidic environments that require heavy resistance to wear. Chemical properties of the material allow for sensitive applications to utilize PEKK parts where outgassing may be a concern such as in combustive environments or sensitive electronic components utilized in aerospace as electric vehicle companies look to diversify their transportation modes.
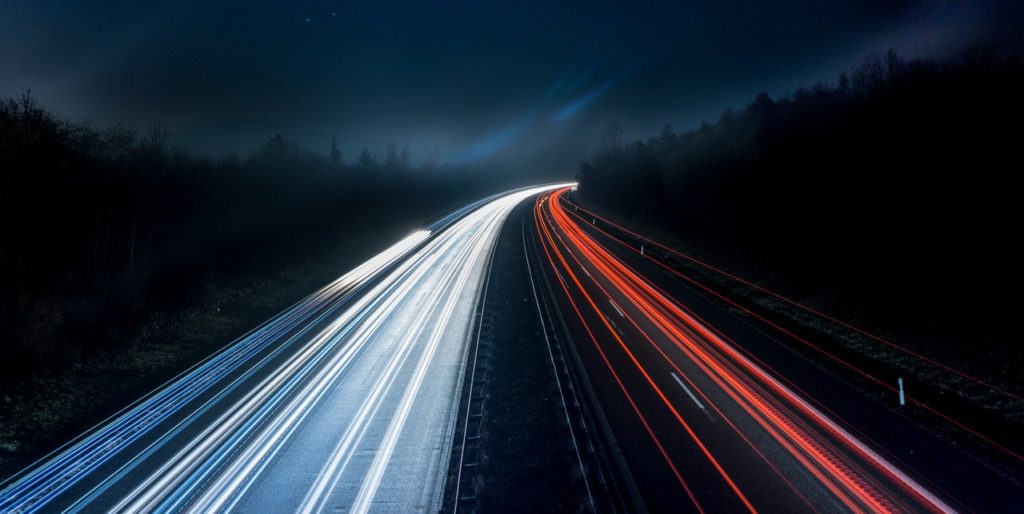
Rapid Axis has had the opportunity to support electric vehicle growth with components manufactured in polyether ether ketone (PEEK), which can sustain continuous high service temperatures of 250°C (482 °F) and is robust enough to operate under challenging conditions surmounted by electric vehicles. Rapid Axis has seen success with machining and injection molding PEEK components. ABS, or acrylonitrile butadiene styrene, provides advanced electrical insulation and is easily printed and machined. In addition to its ease of prototyping utilizing 3D printing, ABS’s postproduction properties allow for improved sanding and paint finishing in production cycles to produce cosmetically and aesthetically pleasing components for electric vehicles. Polycarbonate, a non-conductive polymer, is suitable for use in injection molding and is used currently in electric vehicles for headlight lenses and is ever-expanding into applications where high impact resistance is required and can even be used to produce “bullet-resistant” glass due to its low glass transition temperature and enhanced light transmission properties.
Nylon 12 is a useful polyamide with electric vehicle production where oil resistance is required. Nylon 12 gives parts a high resistance to chemical intrusions as well as a deterrent to stress cracking and abrasion deterioration. Glass Filled Nylon is a moldable composite thermoplastic or thermosetting polymer with high rigidity, mechanical strength, and resistant to shattering. Stainless Steel parts provide HEV, PHEV, and BEV vehicles with excellent corrosion resistance for circuit board transistors provided cathodic protection parameters are controlled by sacrificial anodes if exposed to biological and variable salinity fluids. A significant portion of Rapid Axis’ prototyping and production has historically used Aluminum alloy 6061, which was created in 1935 to construct aircraft fuselages and was recently used to build the Audi A8 chassis. Aluminum 6061, or originally Alloy 61S, readily accepts welding and can be tempered to precipitate a higher yield strength and incredible durability under cyclic loading. Lead times on parts from Rapid Axis consistently have a turnaround of ten (10) business days, which allows electric vehicle development to hum at a pace unseen in the past.
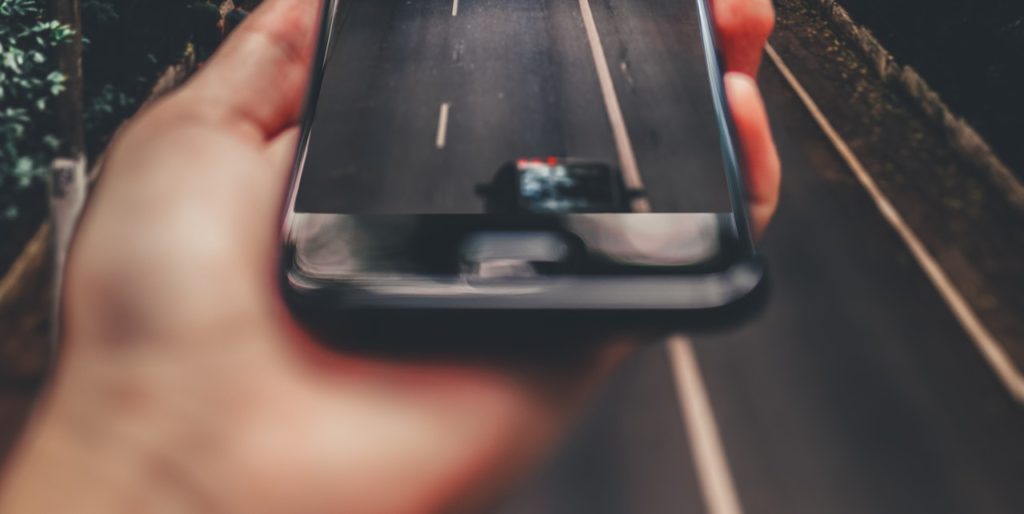
As original equipment manufacturers (OEM) increase demand for BEV, HEV and PHEV components, Rapid Axis has a track record of supporting the industry through collaboration and production of complex components including electric motors, power distribution modules, thermal management systems, and battery packs which often carry as much as half the cost of electric vehicles. By designing and producing rapid component prototypes, Rapid Axis hopes to drive innovation forward and promote the adoption of the new standard of transportation. Electric Vehicle motor components such as DC-DC converters allow electric vehicles utilizing induction motors to provide customers with reliable torque and reduced magnetic loss. The adoption and use of EV motors create a new paradigm of supporting industries in the aftermarket segment by leveraging the compound annual growth rate of nearly 30%, with some reports expecting the global market to reach over $150 billion by 2025.
Not many industries can claim they may grow sevenfold in the next five years. Rapid Axis is proud to support the dedicated engineers and dreamers rushing headlong into what is shaping up to be a lively decade of design and collaboration.