Rapid Axis for Injection Molding
Rapid Axis provides competitively priced, quality parts; quickly. With capabilities in both MUD insert tooling and full family molds, Rapid Axis can be your source for prototype, short-run or production Injection Molding requirements ranging quantity requirements as low as twenty parts and spanning up to one million. Our project by project approach means you’ll get your tooled components fabricated quickly in a mold with a lifespan that suits your project’s needs.
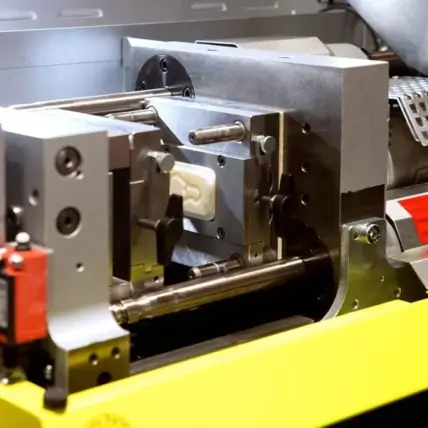
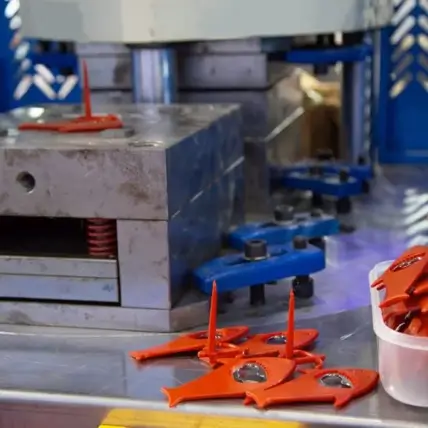
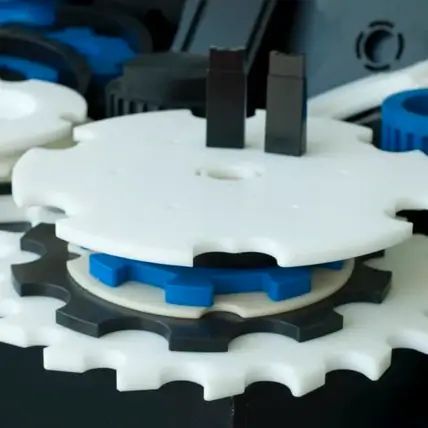
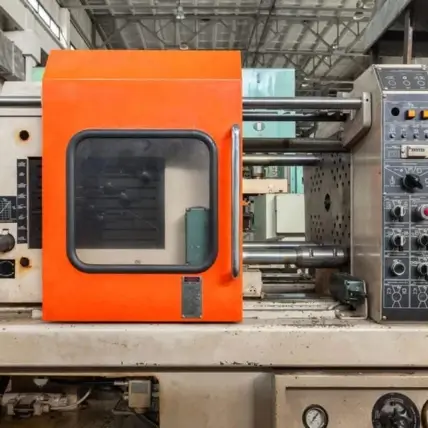
Why Rapid Axis is the best choice for Injection Molding
With multiple presses of various sizes and experience in simple and complex parts, Rapid Axis is the best choice for Injection Molding projects of any size or any volume of parts. We’ve processed everything from gaskets, to gears to enclosures with form in hardware and in a variety of materials from ABS, Polycarbonate, Nylon and HDPE. Rapid Axis includes DFM prior to cutting our tools with mold flow analysis and location for release pins as well as parting lines. Once DFM is approved we’ll run the initial samples for your review and then you can release them for production. This process can take as short as 10 business days and means you’ll get the results you expect out of your Injection Molding project with us.
Short lead times
Great part quality
Thousands of material options
What is Injection Molding?
Injection molding is the gold standard when it comes to mass-producing parts. It has the ability to make a ton of products in a short window of time for a low cost. It’s a form of tooling and molding that’s reserved for high-volume production runs.
The way it works is pretty simple. It starts with a manufactured mold. This is a metal piece that has a cutout that represents the negative of what your product looks like. If you’re making dice, then the mold will have a dice-shaped recess.
The injection molding machine pumps molten plastic. The plastic fills the mold, then sits there for a few seconds to cool and harden. From there, the die is opened, and the part is punched out, freeing up the mold to make the next part.
The entire process can take a few seconds or up to a few minutes — it depends on how large and complex the part is. In either case, it’s a very fast process and it’s highly repeatable.
It’s important that you go with the right shop to make the tooling as well as run the injection molding machine. If the tooling has a minor design flaw, it could lead to defects in the future which will waste your time and money.
In addition, running an injection molding machine isn’t as easy as flipping an “on” switch. You’ll need a shop that has decades of experience running hundreds of different injection molding projects. That’s where Rapid Axis comes in.
Injection Molding Applications
There are a lot of great applications for injection molding machines. If you are considering this manufacturing method for your next project, think about these major benefits and applications.
The Fastest Bulk Manufacturing Available
When it comes to making millions of units a year, there is no other technology that comes close to injection molding. Once a machine is set up, it can run non-stop for days on end, constantly making units.
Besides maintenance and service checks, there’s nothing stopping an injection molding machine from producing more units.
If you compare this to 3D printing or CNC machining, you won’t find nearly the same throughput as you will with injection molding. If you compare the same product being made on all three machines, you’ll see the difference.
In the amount of time it takes for 3D Printing or Machining to fabricate a single component, you can have thousands of parts generated by one of our injection molds.
Here’s the simple way to put it: if you need a ton of units made each year, then you need injection molding.
Inexpensive Per-Unit Costs in Bulk
Injection Molding does require an upfront investment of time and money into tooling and design approval. However, once the tooling is made, you won’t have to worry about it for a long time. A typical mold can last upwards of a million produced units.
When you’re running the injection molding, the per-unit cost is incredibly low. As you order more units, the upfront cost dilutes down and the average cost per unit becomes manageable.
Buying in bulk means getting your unit costs down even lower. Over time, your parts might only cost a few cents each.
However, this raises an important point. You shouldn’t use injection molding if you don’t plan on making a lot of products. If you are considering parts in quantities of tens or hundreds, you should stick with 3D printing or CNC machining. Urethane casting is another nice alternative for smaller batches.
Tooling Lasts a Long Time
As we mentioned, the tooling eats up a lot of the injection molding budget for your operation, but it lasts a long time. Depending on the complexity, geometry, size, and material of your parts, each mold can make upwards of a million products before it needs to be replaced.
Once we dial in the tooling, you don’t have to worry about it again for months or even years.
It’s Repeatable, Consistent, and Accurate
Injection molding offers high repeatability, consistency, and accuracy. Each part will have tolerances as tight as +/-.0005 inches dependent on design and tool type. As the machine creates these parts in bulk, they’ll all be dimensionally identical, and you won’t have to worry about defective parts getting shipped to you.
This technology can make a million parts without having any issues. Since our team at Rapid Axis are injection molding experts, we know when tooling needs to be replaced and when the machine needs to be serviced — just a few ways that we help you get the highest-quality parts at the fastest turnarounds.
Good Material Selection
With injection molding, there are a few different materials to choose from. The most popular options are ABS, polycarbonate, and nylon. Between those three, you’ll find a range of material properties.
We offer all of the market-available options at Rapid Axis, and we’ll help you find the right choice for your project.
This manufacturing option doesn’t boast the same breadth of choices as 3D printing or urethane casting, but it offers a throughput and price that the other two options can’t come close to.