Rapid Axis for Prototype Injection Molding
At Rapid Axis, we understand the critical importance of accurate and cost-effective prototyping during the product development process. Our prototype injection molding services are designed to help you test, iterate, and perfect your designs before committing to full-scale production.
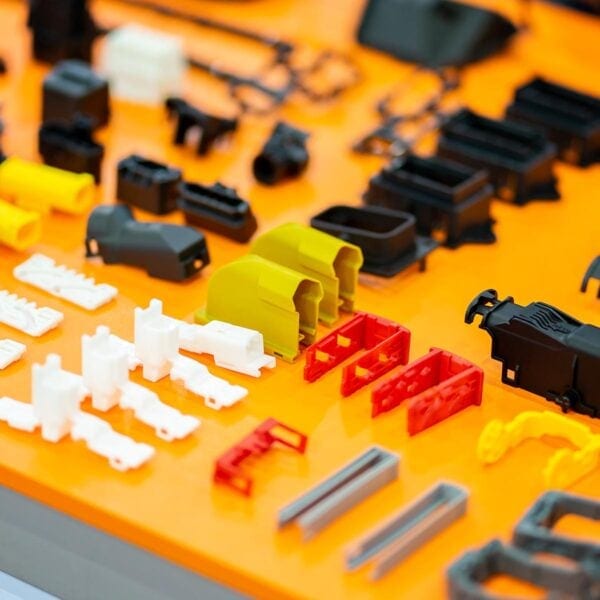
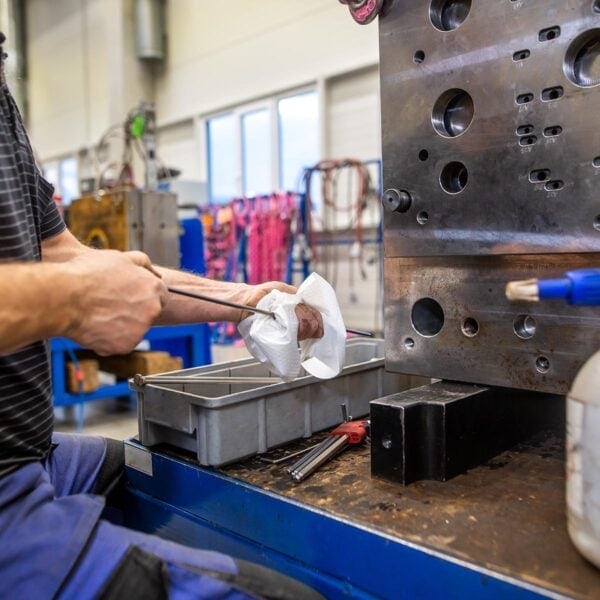
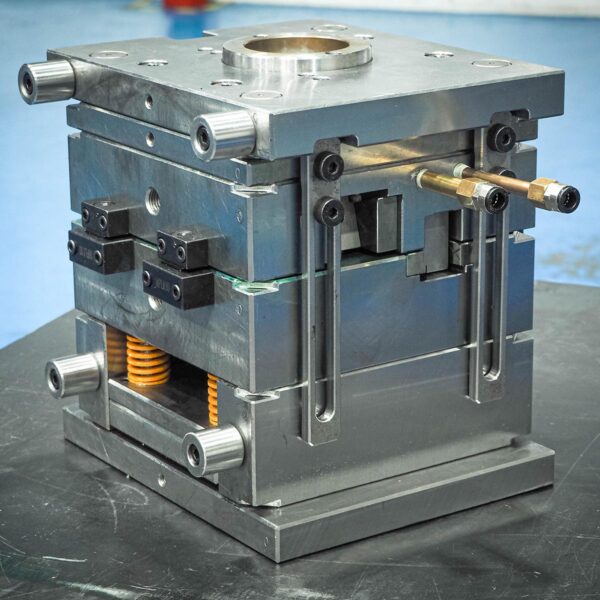
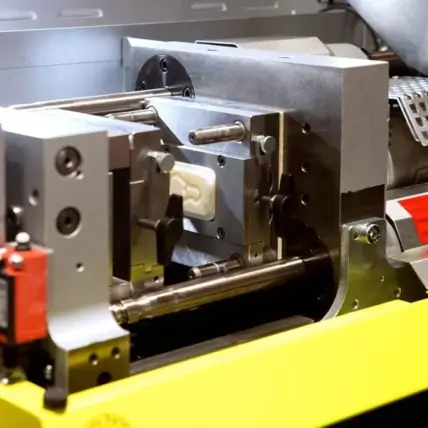
Why Choose Rapid Axis for Prototype Injection Molding?
When it comes to rapid prototype injection molding, Rapid Axis offers unique advantages that make us the ideal choice for your manufacturing needs. Our dedication to quality, efficiency, and customer satisfaction ensures that every project is handled with the utmost care and precision.
Short lead times
Great part quality
Thousands of material options
Precision, Efficiency, and Expertise in Prototype Injection Molding
From simple plastic components to intricate assemblies with tight tolerances, our advanced facilities and skilled team will ensure your prototypes are delivered on time and meet your exact specifications.
With years of experience in plastic injection molding, we pride ourselves on offering a seamless process from design to finished part. We combine cutting-edge technology, diverse material options, and expert craftsmanship to provide a level of quality that sets us apart from competitors. Whether your goal is to validate a concept, test the functionality of a design, or ensure compatibility with other components, Rapid Axis can be your trusted partner.
Our approach is rooted in speed, flexibility, and precision. By leveraging the latest advancements in prototype injection molding, we help businesses in industries such as aerospace, automotive, consumer goods, and medical devices take their ideas from concept to reality with minimal risk and maximum efficiency.
This means parts are delivered faster to your loading dock with fewer issues when you choose Rapid Axis.
Key Benefits of Rapid Axis Prototype Injection Molding
Why do companies across the country choose Rapid Axis? Our prototype injection molding services offer a ton of unique benefits:
Fast Production Times
Speed is essential in prototyping, and Rapid Axis excels in quick turnaround times. Getting your part to market too late can mean losing to your competitors, and we never want that to happen.
Our streamlined processes, advanced machinery, and expertise allow us to deliver high-quality prototypes in record time. For companies under tight deadlines, our rapid prototyping capabilities can ensure your project stays on track. Whether your design is right on the first try or you need a dozen iterations, we can help you breeze through the prototyping phase and get to production faster.
Cost-Effectiveness
Prototyping is about testing and refining without the expense of full-scale production tooling. Rapid Axis uses cost-efficient materials and production techniques tailored for short runs.
This minimizes your upfront investment while ensuring you receive high-quality prototypes that accurately represent the final product. By focusing on efficiency, we help you save money during the critical early stages of development.
These lower upfront costs are going to be a lot more palatable for your stakeholders and investors.
Diverse Material Selection
The choice of material can make or break a prototype’s success. Rapid Axis offers a wide range of material options, including engineering-grade plastics, thermoplastics, and specialty polymers. Our team works closely with clients to recommend the best materials based on the application, ensuring the prototypes perform as expected under real-world conditions.
If you’re not sure what material is right, give us a call and we can discuss it together. Otherwise, we can make the same prototype out of multiple materials so you can see for yourself which is the perfect option for your upcoming production run.
Iterative Design Support
One of the key benefits of prototype injection molding is the ability to iterate on designs. Whether you need small adjustments or significant changes, Rapid Axis supports multiple design iterations to refine your parts.
This iterative approach reduces the risk of costly errors during full-scale production. By catching any design issues earlier, you can avoid massive impacts on your timeline and budget in the future.
Comprehensive Quality Assurance
Each plastic prototype undergoes rigorous quality checks, including dimensional analysis and functional testing. By prioritizing quality at every step, we ensure your prototypes meet exact specifications and are ready for real-world testing.
Expert Guidance
Rapid Axis provides expert support throughout the process, from initial design to final delivery. Our team’s deep understanding of plastic injection molding ensures that every decision — from tooling design to material selection — is optimized for success.
Part of choosing the right injection molding company entails working with an experienced partner like Rapid Axis who can make your life easier.
What is Prototype Injection Molding?
Prototype injection molding is a specialized manufacturing process used to create small quantities of parts for testing and validation purposes. Unlike full-scale production molding, which focuses on high-volume runs, prototype injection molding is tailored for rapid, low-cost production. This allows engineers and designers to evaluate the functionality, form, and fit of their designs before committing to large-scale production.
Key differences between prototype injection molding and production molding include:
- Lower Production Volumes: Prototype molds are designed for shorter runs, making them more cost-effective.
- Simpler Tooling: Prototype molds often use less expensive materials, such as aluminum, reducing lead times and costs.
- Flexibility: Prototyping allows for quick adjustments to design, materials, or processes.
Prototype injection molding is widely used for applications like functional testing, design validation, and creating proof-of-concept models. It is an essential tool for industries requiring precision parts, such as medical devices, aerospace, and consumer electronics.
Prototype Injection Molding Applications
Prototype injection molding serves a variety of industries and applications, enabling companies to reduce risk and optimize designs before full-scale production. By using prototype molds, engineers can evaluate parts in real-world scenarios and ensure they meet performance requirements.
Common Applications for Prototype Injection Molding
A lot of people choose Rapid Axis for our prototype injection molding services. If you’re not sure how this service can work for you, consider these common applications:
Functional Testing
Prototypes are used to assess how a part will perform under expected conditions. For example, automotive manufacturers might test the strength and durability of interior components, while medical device companies evaluate the functionality of device housings.
Design Validation
Ensuring that a design meets dimensional and performance requirements is critical before moving to production tooling. Prototype injection molding allows designers to identify and correct issues early in the process.
Form and Fit Testing
Prototypes help confirm that parts will assemble correctly with other components. For instance, aerospace engineers might test how a molded part integrates with other systems to ensure proper fit and function.
It’s Repeatable, Consistent, and Accurate
Companies often use prototypes to demonstrate new product concepts to stakeholders, investors, or customers. This helps build confidence in the design and functionality of the final product.
You can also utilize injection mold services for any projects that require precise custom parts.
The Prototype Injection Molding Process at Rapid Axis
At Rapid Axis, we follow a proven custom injection molding process to ensure every prototype meets the highest standards of quality and precision. Our team works closely with you at every stage, offering expert guidance and support to bring their designs to life.
1. Consultation and Design Review
The process begins with a thorough review of your design. Our team can perform a Design for Manufacturability (DFM) analysis to identify potential issues and optimize the design for molding.
2. Tooling and Mold Creation
Using advanced software and machining techniques, we create prototype molds tailored for short runs. These molds are typically made from aluminum, which reduces lead times and costs.
3. Material Selection
Based on the application and performance requirements, we can help you choose the best material for your prototypes. This step ensures the final parts meet all functional and aesthetic criteria.
4. Injection Molding
The selected material is injected into the mold cavity, creating accurate, high-quality prototypes. This process is optimized for efficiency and precision without costing you too much.
5. Quality Assurance
Every part undergoes rigorous quality checks to ensure it meets specifications. Our quality checks include dimensional analysis, material testing, and performance validation.
6. Delivery
Once the prototypes pass all quality checks, they are carefully packaged and delivered to your facility.
Our comprehensive approach to plastic injection molding ensures that every part is produced to the highest standards.