Rapid Axis for CNC Turned Parts
With unique equipment formats and high speed turning capabilities, Rapid Axis is an easy choice for CNC Turning. Our offering of competitively priced, quality parts; quickly will keep Rapid Axis on your supplier list year after year. Almost no project is a “no quote” and we can build CNC turned components both large and small.
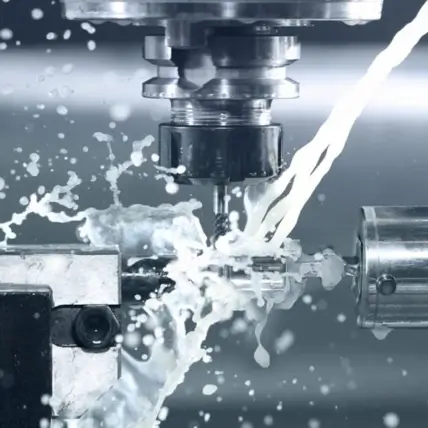
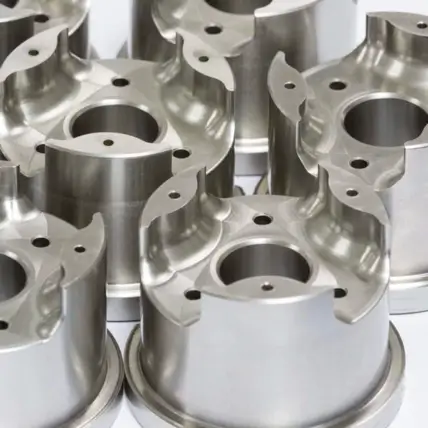


Why Rapid Axis is the best choice for CNC Turned Parts
With consistent reliable quality, excellent pricing and best in industry customer service, Rapid Axis is the clear choice for your next CNC Turned parts. We offer free 1st Level Inspection on all projects and quotes to match print without blanket statements about loosened tolerances. With no minimum quantity and quick lead times, we can take you from prototyping to production for any turning project. Our best in industry customer service and competitive pricing will keep you coming back for everything from a simple turned aluminum housing to a hardened steel valve.
Parts made to match customer tolerances
Support both small and large turning operations
Finishing and second operations supported
Technical
General Tolerances: Easily +/-.002 or tighter, matched to drawing
Build Size: Turning 32” Diameter
Finishing and 2nd Operations: Anodize, PAA + BR127, Powder Coat, Paint, Chem Film, Alodine, Chromate, Heat Treating, Black Oxide, Zinc Plating, Polishing, Bead Blast, Electropolish, Gold Plating, Silver Plating. Brushing, Vapor Polish, Teflon Impregnation, Park Marking, Logo Work, Hardware Installation, Assembly and more
See Finishes page
Equipment: HAAS, FADAL, CONQUEST, OKUMA and more
Materials: ABS, Acrylic, Aluminum, Copper, Bronze, Brass, Delrin, FR4, Garolite G10, HDPE, Inconel, Magnesium, Noryl, Nylon, Polycarbonate, PEEK, Polypropylene, PTFE, Stainless Steel, Steel Alloys, Titanium, UHMW PE, PVC, Zinc and more
See Materials page
What is CNC Turning?
CNC turning is a form of fabrication that involves the use of Computer Numerical Control (CNC) machinery. A turning machine is a little different than some of the other CNC machines such as mills you may already be familiar with.
One of the most common forms of CNC turning is a CNC lathe. With a lathe, a chuck is tightened on a piece of (typically) cylindrical material. The chuck then spins incredibly fast while a stationary cutting tool is moved into position. The tool cuts away material from the cylinder.
Since the piece is rotating, the cutting operations are done symmetrically around the central axis of the part. This makes it easy to change overall dimensions and cut symmetric features on a rounded object.
The addition of CNC operations on these turning machines can help a lot. The machinist has access to a controller with various feature assignments and they will get exact readouts from the screen and be able to use the position to make different cuts.
More advanced CNC lathes at Rapid Axis can be completely operated by just using the controller. In some cases, the lathe is a large, enclosed machine. Inside, the turning machine can automatically change out tools, make cuts, thread the part, and have the cutting head rotate around the part.
With these advanced systems, the precision, turnaround time, and quality of the parts created are more desirable. People tend to choose CNC turning whenever they’re working with cylindrical parts — things like housings, linear actuator parts, valves, rotor shafts or any radial component.
CNC Turning Applications
To better understand if CNC turning is right for your project, we put together this section. We’ll discuss some of the major reasons why people choose CNC turning, and some benefits of this manufacturing option.
Great Precision
Between the mechanical nature of a lathe and the addition of CNC capabilities, CNC turning machines offer very impressive precision. At Rapid Axis, we can machine features within +/-.0005”, sometimes even tighter, on our lathes.
This means that you can get CNC turned parts that fit perfectly into your operation or assembly, every time. We’ve had clients that were buying stock pins that simply weren’t fitting into their assembly. Rather than rebuild the assembly, we created custom pins by cutting the outside diameter. After we delivered the order of precision parts, the customer never had a problem again with the fitment.
Ability to Reliably Work on Cylindrical Parts
There are very few ways to reliably work on rounded or cylindrical parts in a machine shop. To mill them, you would need to buy custom chucks and retrofit them. The best way to machine a cylinder is with a CNC turning machine.
A CNC mill can make circular features, but it runs on a 3-axis linear system. That’s like making a circle on an Etch A Sketch (but much more precise) — making truly circular features is very difficult. CNC lathes are designed to make truly circular features and work on circular objects.
Very Fast Turnaround Times
CNC turning machines offer incredibly fast turnaround times as compared to other fabrication methods. If you need a dozen 1-inch-long rods that have a certain inner dimension and outer dimension, it couldn’t be easier with a CNC lathe.
A full 2-feet of material could be turned quickly to get the right inner and outer dimensions. From there, we can slice the material every inch, leaving you with 24 units from a single part in just a few hours of machining time.
Even with more complicated parts, a programmed turning center makes everything much faster since it has CNC controls built in.
Drilling Holes with Very Tight Tolerances
If you have a part that needs a very specific hole size, you can either bore it or turn it. A typical drill press’s bit will chatter and vibrate as it makes holes. With a good CNC lathe, holes can be made to very tight tolerances. The only caveat is that the hole needs to be along the central axis of the part.
A good example of this is if you imagine a metal cylindrical sleeve — a rod with a thru-hole. If the thru-hole has to fit over an existing part within a few microns, it might not be possible with a standard drill press or milling machine. With a lathe, not only is it possible, but it’s easy to do for a trained machinist.
Quickly Adding Rounded Features
Other people have parts that they just want to round off or deburr. A machinist might use a belt sander, but it often gives an uneven finish — especially for circular parts.
With a CNC turning machine, a machinist can quickly add a fillet, chamfer, or radius to a circular part with very little effort. In a lot of cases, the longest operation is setting up the machine and putting the material in the machine’s chuck.
A part can be rounded and deburred in just a few seconds on a lathe.
Creating “Rough Cuts” for Later Operations
Other times, it makes sense to use a lathe as the first step of a manufacturing operation. If you need a series of cylindrical blocks that have off-center internal cuts and square features, you would need to do the machining on a CNC mill. However, you can use a CNC turning machine to quickly create a rough cut before putting it on the mill.
The lathe can create the perfect outer dimension, inner diameter, and total thickness of a part before it moves to another machine. Doing the same operation on a mill would take much longer, and it might not even be possible depending on the size of the part.