Rapid Axis for COTS Machining
Rapid Axis is happy to take on traditional job shop work and modify your off the shelf hardware whether it’s machining of McMaster Carr, Grainger or other source hardware. We’ll take a look at your drawings and quote accordingly for your manual machining operations.
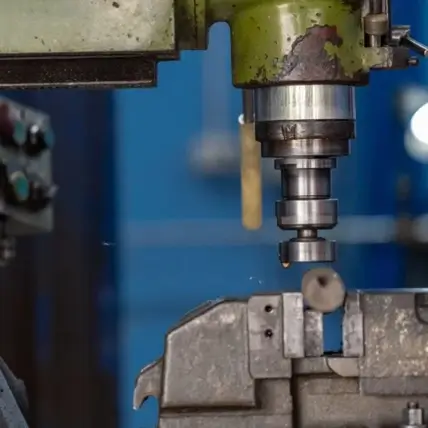
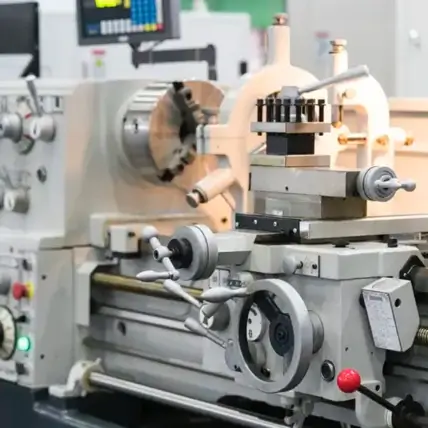
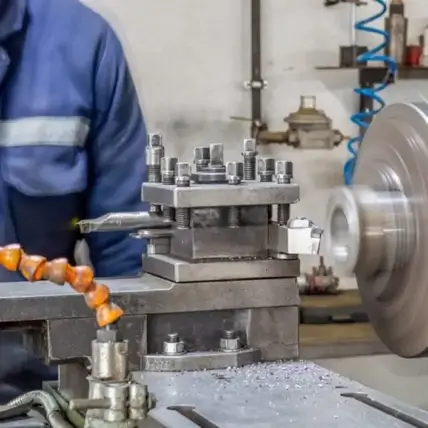
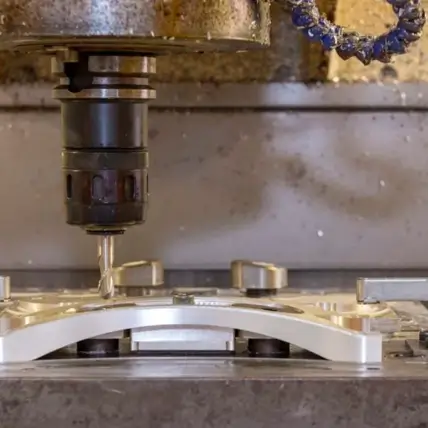
Why Rapid Axis is the best choice for COTS Machining
With a full equipment line up including automated and manual mills & lathes we have the equipment and solution needed for your off the shelf component machining. Anything from simple holes drilled and tapped to complex multi-axis machining operations, Rapid Axis can support. With high responsive quoting and communicative project management you can rest assured your hardware modification project is in good hands.
Parts made to match customer tolerances
Finishing and second operations supported
3, 4 and 5 Axis Milling supported
What is COTS Machining?
Commercial off-the-shelf (COTS) machining goes by a few different names: second (2nd) operation machining, or manual machining. Regardless of what you know it as, the concept behind this style of manufacturing is the same.
COTS machining entails taking an off-the-shelf item and doing some form of machining to it before introducing it to your operation.
For instance, you might take a standard mounted sleeve bearing and drill new holes in it to fit your operation. You might want a shaft collar of a certain internal dimension with an additional keyway machined in.
In either of these cases, you’ll purchase a standard commercial part then go through a secondary round of machining to make it perfect for your operation. It’s a less common ask from our customers, but we always get excited when we get to quote a COTS machined part.
From a machine shop’s perspective, there are more considerations that come into play. Sometimes jigs need to be made for workholding a commercial part. Other times, we need to get creative with how we clamp and work on a part.
There are plenty of COTS items that come with treatments on them already. That means that our experts need to understand how to work with the treatments and what finishing steps to do after drilling to fully coat the part again.
At Rapid Axis, you can either ship the COTS item to us or give us the product details so we can order it directly. With the COTS item and a design provided by you, we’ll use CNC machining to create the perfect part.
COTS Machining Applications
This concept might be a little strange to understand at first. To better explain how it works and why people choose COTS machining, we put together this quick section of applications. We’ll also include some benefits of using COTS machining instead of making parts from scratch.
It Saves You Money
When it comes to machining complicated assemblies, the price can add up pretty quickly. The more difficult it is to make, the more expensive the part is.
One way to save money is to choose COTS machining instead. Since the original manufacturer is making this product in bulk, their price to make it is much lower. That means that it’ll be less expensive for you to buy it than to try to reverse engineer and replicate it.
Instead, you’re just paying for the additional operations like drilling and cutting the part.
Not only does it save you time during manufacturing, but it saves you engineering time. Finding a part and reverse engineering it can take days or weeks, depending on the part. It might also include sourcing additional parts used in the assembly. All of these man hours add up to a lot of money wasted.
With 2nd operation machining, all of these hours can be saved. Instead, you’ll just find the part from a brochure and design the changes you’d like done. Just like that, you saved days of hard design work.
To put it simply, COTS machining can save you money during every step of the process.
Experience Faster Turnaround Times
In addition to saving money, you’re saving a lot of time. As we just highlighted, reverse engineering can take a lot of time. On top of that, machining a part from scratch can be a time-consuming process. Creating programs and executing them on one-off parts requires a lot of upfront effort.
With COTS machining, the longest lead time is typically just waiting to receive the part from the supplier. The actual machining steps are often very simple, quick, and easy to do. Since we have a lot of COTS machining experience at Rapid Axis, our turnaround times are even more competitive.
Create Intermediately Sized Parts
When it comes to manual machining, there’s a large opportunity to hand-craft a part that exists between two standard sizes in the seller’s catalog. As a very simple example, picture a 1/4-20 socket head cap screw. They’re sold in nominal sizes like 1”, 1-1/4”, 1-1/16”. But, what if you want a non-nominally sized bolt for your assembly?
Let’s say you want a 1.119” long 1/4-20, a non-nominal size. Instead of changing your whole assembly so that a 1-3/16” bolt works, you can have us grind down a standard bolt to the new dimension.
This example was overly simplified, but the same idea can be applied to a number of different product lines. If you’re shopping for a part in your assembly and you fall between two different part sizes, there’s a chance that we can help you get the perfect product with COTS machining. This is what we mean by creating intermediately sized parts.
Avoid Redesigning Your Process
At the end of the day, people choose COTS machining in an effort to avoid redesigning their process or assembly. It’s a lot easier to machine a purchased part than it is to resize your assembly to fit the part.
In some cases, it’s downright impossible to redesign the assembly. This is true for any operation that has a legacy or mature design. Even if it is possible to change the assembly, it might require months of additional work to fix all the other problems associated with doing that.
The better solution is to let Rapid Axis do some COTS machining to achieve the perfect part.