Rapid Axis for PolyJet
Rapid Axis provides competitively priced, quality parts; quickly. With large format Objet machines at our disposal, Rapid Axis is well suited for prototype and production polyjet projects alike. Rapid Axis keeps most commonly processed materials available on demand such as black ABS-like, clear and elastomeric materials.
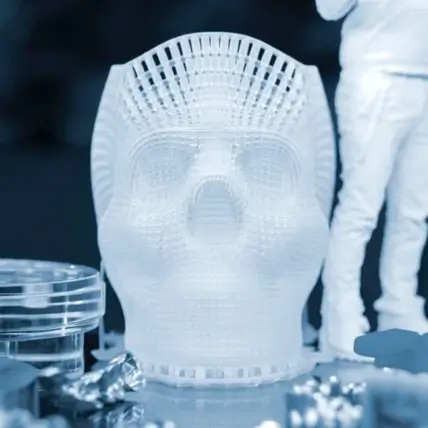

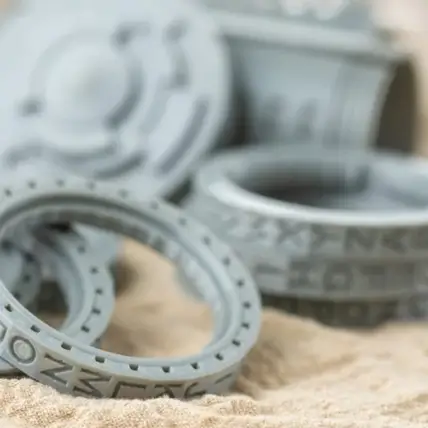
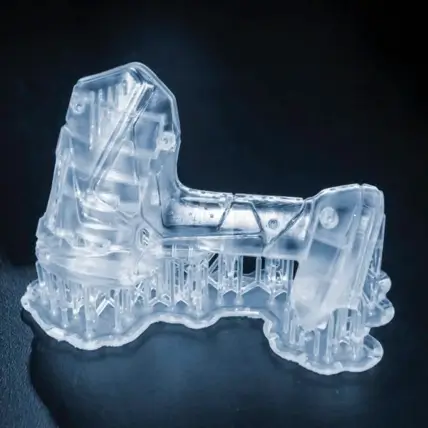
Why Rapid Axis is the best choice for Polyjet
With lead times as quick as 1 business day for Polyjet it’s no surprise that Rapid Axis is one of the quickest shops offering this service line. We have several large format Objet Polyjet printers at our disposal and they’re often just waiting for your hot project to come in. We can consult on quick prototypes and appearance models alike. Just reach out to one of our team members and see why Rapid Axis is the best choice for all your Polyjet needs.
Short lead times
Cosmetic models
Excellent support
Technical
General Tolerances: +/-.005” for the first inch, +/-.001 each inch after
Build Size: 19.” x 15.4” x 7.9”
Cosmetics: Print clear, print in color, bead blast, polish, paint and dye
Equipment: Objet
Materials: AGILUS30 Clear, AGILUS30 Black, Digital ABS/ABS2, Flexible Materials, Durus, Vero, Vero HQ, Rigur, Med610
See Materials page
What is PolyJet Printing?
A PolyJet 3D printer works a lot like your desktop inkjet paper printer, but with some extra science. Like other 3D printers, there is a head that moves across a build area. In this case, the build area is a platform filled with a photopolymer resin. Photopolymers are sensitive to UV and visible light, and they’ll react once they come in contact with light.
As you might expect, this printer uses light to its advantage. The head will move from side to side, laying down a single layer of resin. The resin is placed in areas that will later become part of the 3D part, so the machine is essentially tracing the part layer after layer.
The other thing to point out is that the resin can be different since there are multiple heads jetting it out. This means that a single part can have two or more physical properties and colors within a single part.
Not only does the head have a number of resin jets, but it also has a UV curing light. As resin gets deposited, the light activates and starts hardening the dropped resin. This means that every layer gets “baked” by the light and fused to the previous layer as the machine keeps going.
Once one layer is done, the print head will move up a layer and repeat the process until the full part is done.
PolyJet Printing Applications
This is one of the more intricate 3D printing options on the market, so we understand that it’s tough to understand. To make things simple, we’ll talk about some common applications and benefits of PolyJet printers. This should help you gauge if this technology is right for your upcoming project.
Print Specific Durometers
One of the key features of a PolyJet printer is that you can specify exactly what durometer you want your part to have. If you didn’t know, the durometer of a part is how soft or hard it is, and it typically refers to rubbers.
Low durometers are softer, more flexible, and easier to move around. We have customers in the robotics and medical device industries that rely heavily on our PolyJet rubber printed parts.
To make rubber parts otherwise, you would need to use an injection molding application which requires you to order hundreds or thousands of a unit. To use a CNC machine, tool speeds need to be dramatically reduced, and you need to pick a shop that has specific experience working on rubber.
It’s hard to explain exactly how useful PolyJet printing is, given that information. It fills the gap and allows us to run small-batch orders of rubber parts for our customers.
Mix and Match Material Properties
As we mentioned, the head of a PolyJet printer can deposit different material concentrations within the same part. That allows you to get creative with the design of your product.
You can have the exterior be extremely rigid while the inside is flexible. When it comes to fitments, the ability to change how rubbery certain sections are will help you assemble parts together.
It also helps people who want to make consumer goods. Since you can have different colors in the part, you can print logos and designs directly in the part. The best part is that the design can’t be simply wiped away, since the part was created using these different colors. Suddenly, you can take your branding to the next level and create customized merch.
Easily Prototype Silicone Rubber Parts
When it comes to 3D printing rubber parts, FDM and MJF printers offer a lesser version of what the PolyJet can create. In other words, PolyJet printers outshine any other form of manufacturing when it comes to small-batch rubber parts.
Our customers customarily choose PolyJet printing when they want to prototype a part that will later be injection molded out of silicone rubber. For reference, prototyping and changing designs with injection molded parts is borderline impossible. Once the master mold is made, nothing can change (besides the material selection) without a massive cost associated with it.
How are you supposed to prototype and change your design before paying for the master mold? This is where PolyJet-printed parts come in. From a material properties standpoint, they’re identical to a silicone rubber part. You can prototype and iterate a part with a PolyJet printer to perfect the design before buying the injection molding tooling.
The Final Detail Is Impressive
We should also point out that the detail and precision we can achieve with our PolyJet printers are downright impressive. We can print in layers as fine as 0.0018″ thick, with tolerances as low as +/- 0.004” for the first inch is typical, plus +/- 0.002” for every inch thereafter, and achieve a very smooth finish on each part.
This is the case without the need for any finishing. In other words, you can get a smooth part faster since we don’t have to sand it down and make it smoother.