Rapid Axis for 3D Printing
Rapid Axis provides competitively priced, quality parts; quickly. We provide quicker speed to market within your product design lifecycle with quick turn, industry trusted 3D Printing methods. Work with Rapid Axis for short lead times, production grade materials and the best customer support in the industry. We are dedicated to delivery and service on your project!
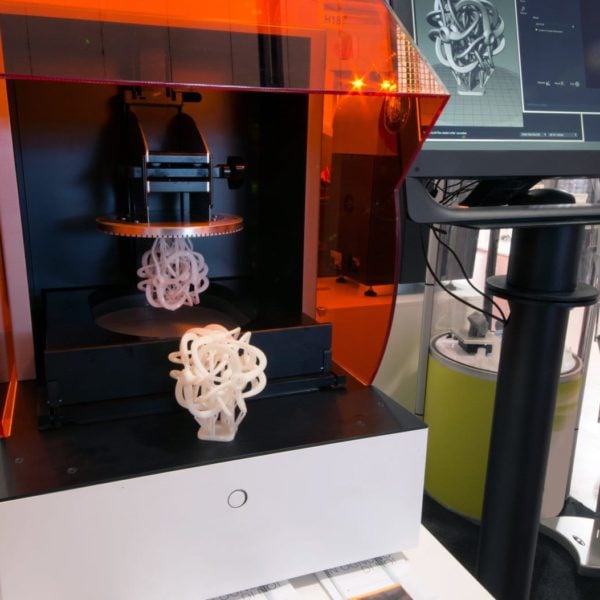

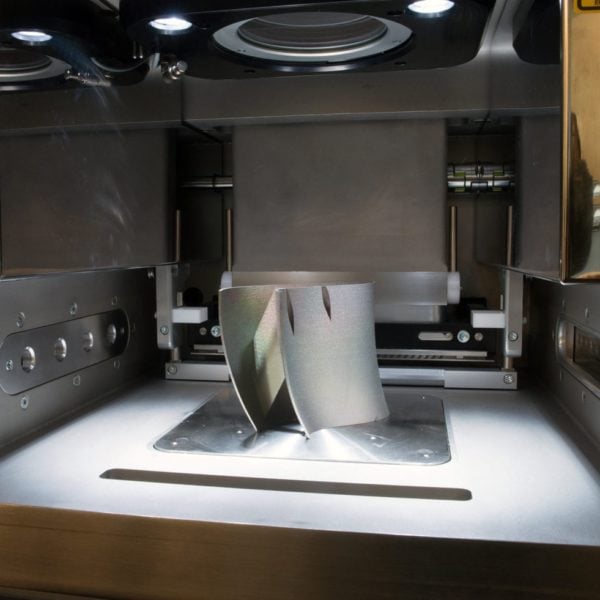
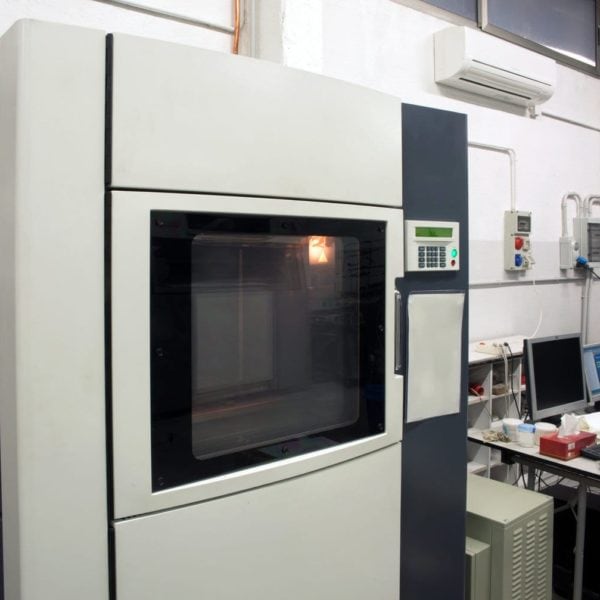
Why Rapid Axis is the best choice for 3D Printing
Rapid Axis has a superior focus on quality and customer support beyond that of a traditional 3D Printing service bureau. Rapid Axis staff has a combined 100 years of experience in 3D Printing and can consult or advise on almost any question. With a versatile equipment format, finishing capabilities and excellent quality control you can expect your next 3D Printing project to go off without a hitch when you choose us. With Rapid Axis’s dedication to support and quality we’re an excellent candidate to take on either your Prototyping or Production 3D Printing work.
Parts made quickly
Excellent post project support
Production grade materials
What is 3D Printing?
3D printing is a relatively new style of fabrication. It involves building products via the method of Additive Manufacturing, where parts are made one layer at a time. After all the layers are created, you’re left with a real-life version of your 3D CAD model.
If you pick up any product near you and imagine it was cut into a thousand slices, you’ll understand the concept behind 3D printing. Regardless of the style used, each one builds an item one layer at a time. This allows for quicker builds as well as features not typically allowable by other manufacturing methods.
Engineers turn to 3D printing for fast, low-cost prototyping units as well as production units that do not require tooling or cannot be fabricated by other methods. Rapid Axis supports both Production and Prototyping within 3D printing and will build quantity.
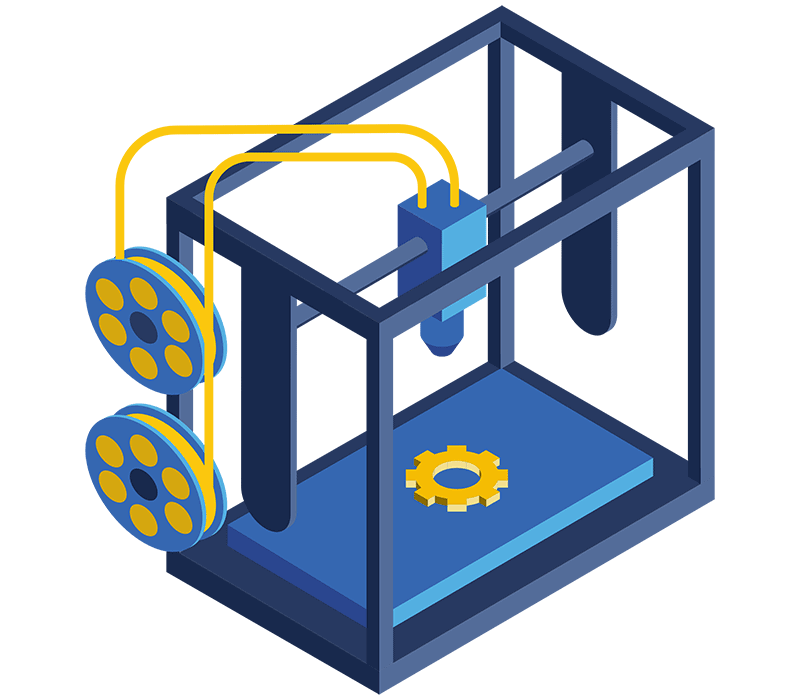
Different Types of 3D Printing at Rapid Axis
Rapid Axis supports the following 3D Printing technologies.
FDM
FDM is what people typically picture when they think of 3D printers. These machines can be desktop or large units that use plastic filament that gets melted and extruded through a heated nozzle. It is widely used for prototyping and production applications. Production grade materials including thermoplastics are available.
SLS
In an SLS printer, a laser is used to sinter the part out of layers of nylon-based powder. The distinction between this option and MFJ is the addition of a laser. SLS results in more wasted material, but it’s less expensive and has a slightly worse finish than MJF though SLS benefits from not having the addition of a binder agent. Many SLS materials are medical grade or approved for flight applications.
SLA
SLA is a high-precision, high-quality 3D printing option. A tub is filled with a liquid thermoset resin. A laser uses ultraviolet beams to image one layer of the part that’s being printed. Another layer of resin is added on top, and the process continues. The parts might emulate other materials, but they’re always made from a UV curable resin. From SLA you can get high resolution builds that behave like known materials but typically will degrade over time.
3D Printing Applications
As you notice, there are a lot of different 3D printing options we offer at Rapid Axis. That’s largely because all of these printers are highly versatile and have a lot of applications. You can learn more about the benefits of each specific style on their pages, but here are some general benefits of 3D printed parts:
Fast Prototyping
3D printers are the king of prototyping. We can start a 3D print before leaving for the day, and when we return to the office, we’ll have a fully functional prototype ready to ship. Depending on the quality, size, and material you choose, you can have a prototype within a few hours. Sometimes Rapid Axis can support one business day lead times.
These prototypes can be used for fitments, as production parts, proof of concept, and act as a visual aide for stakeholders. Since they can be printed so quickly, it’s easy to iterate a design and keep printing new versions.
Low-Cost Trial Runs
Another thing to consider is the cost associated with each 3D printed part. With more traditional prints on an FDM, a parts cost is mostly associated with its volume of material. For more complicated parts and production-quality items, it’s still much less expensive for 3D printing as the machine itself is doing the work and no human labor is required.
Comparing this to a CNC machined part, the difference can be staggering. CNC machines require a lot of upfront work to program, set up, and start the machine. Once the program is written, subsequent parts are faster. However, single-part runs can be very expensive.
With injection molding, trial runs aren’t even an option. Tooling costs are so high that it won’t make financial sense to make a handful of parts.
Any time you want to make a low-run batch or trial run, you should start off by considering Rapid Axis for 3D printing.
High Precision and Accuracy
3D printers offer some of the most impressive precisions across the entire machine shop. By slowing down the printer and adding more layers, the final accuracy can be less than .005” overall. That same tolerance would take much longer and be much more expensive through machining or other methods.
These tolerances fall into a separate category in traditional machining, and they’re classified as “high precision” — in 3D printing, it’s standard.