Intro
When it comes to prototyping, there are a few different options to choose from; CNC machining, 3D printing, and injection molding. When it comes to medium-batch or short-run production runs that are affordable and fast, then quick turn injection molding becomes the best option.
In this piece, we’ll talk all about prototyping with injection molding. We’ll teach you what it is, how it works, and some benefits of this manufacturing option.
What Is Injection Molding?
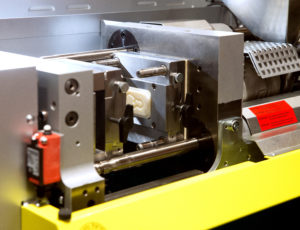
Injection molding is a style of manufacturing. In this option, a hollow mold is filled with molten material. The material fills every crack of the mold, then it sits there for long enough to cool and harden.
Once that happens, the mold opens up and the part can be removed. The mold will close and get ready for the next stream of molten material and the cycle continues
The whole process might only take a few seconds or minutes (depending on the complexity and material choice). Each time the process happens, you get a usable unit of your designed part.
How the Process Works
Our quick turn injection molding uses the same concepts as full-scale injection molding, but the costs and stakes are much lower. A full-scale operation will use hardened materials for the mold that can create upwards of a million parts.
With quick turn injection molding, softer materials are used for the mold that might only last a few hundred or thousand times before they need to be replaced. Typically, a molding insert will only be made, this is a single cavity insert that goes into a pre-existing tool setup. It allows for quick change out of inserts to run parts quickly.
Since prototyping injection molds are less temporary, they’re also less expensive, easier to make, and offer faster turnarounds.
You would provide a 3D model of what you want your final part to look like, tolerance specifications, and material characteristics, and the mold fabricator would handle the rest.
Benefits of Using Injection Molding for Quick Turns or Prototyping
To better understand how injection molding might benefit your prototyping project, let’s review some of the major benefits. These are benefits that we’ve personally seen over the years.
Use the Right Material
A 3D printer is another great solution for prototyping, but they have material limitations that make it hard. After all, you need a prototype that will act like the final version of the part, and a large factor is the choice of material.
With injection molding, you can choose from a wide variety of different material choices. This will ensure you get a “real-world” version of your part.
Medium Quantity Production or Prototype Runs
Another place where injection molding shines is when it comes to medium-sized quantities. This would be anything in the 10s to 1,000s range though sometimes these tools are good up to several hundred thousand.
In other words, if you want 100 to 1,000 parts to work with, then quick turn injection molding is probably the right choice.
All of the parts will be dimensionally and functionally the same. You can have them made in different materials or color options to see which one is right for you.
People might make this many prototypes to show stakeholders, use for demonstrations, or put the parts through testing. With 3D printing or CNC machining, you won’t get the same affordability, turnaround time, or quality.
Allows for Real-World Testing
When it comes to bringing a new product to market, you will likely go through several rounds of testing. From cyclic testing to stress testing, you need to make sure you have enough units to get the full scope of how well your parts perform.
Since injection molding will create production-grade versions of your parts in larger quantities, you can easily test your parts until they fail without an issue.
Running the same tests on a 3D-printed part might mean wasting time and getting results that aren’t usable.
It’s a Low-Cost Option
Injection molding is the gold standard when it comes to mass-producing units at affordable prices. During the prototyping stage, it’s the same story.
You can get 100 parts quickly and more affordably when you choose injection molding rather than other manufacturing options.
As you scale up your production, your per-unit cost gets even lower. It’s common for mass-produced parts to only cost cents. During the prototyping stage, the costs might not get that low, but they’re still going to be more affordable than CNC machined parts in the same quantity.
The Risk Is Lower
A lot of times, the mold machinist will use a soft metal or hard plastic to create a prototyping injection mold. This allows them to go in and make iterative changes as your design matures.
For full-scale production, the mold is made out of a hardened material that is very difficult to change.
By using softer material options, your risk is lowered. You’ll be able to change the design of your parts without having to make brand-new molds — this saves you a lot of money and time.
If you choose injection molding for your prototyping phase, you can go through iterative designs and fine-tune your final product before making the master mold.
Conclusion
Our manufacturing experts just discussed what prototyping injection molding is, how it works, and some major benefits. If you’re considering using injection molding or you want to learn more, you can reach out to our team at Rapid Axis. We handle all of the manufacturing steps, so you don’t have to worry about anything. Get a free quote from us today to get started.