Intro
In a lot of cases, plastic is the hardest-working material. In almost any industry, there’s at least one application where plastic does a much better job than metal or wood. Still, people don’t understand how plastic can be machined or used.
In this guide, we’ll explain how plastic can be machined, when to use it, and considerations that machinists need to make.
How Can Plastic Be Machined?
Even though plastic can be difficult to work with, you can work on plastic through a number of different machining techniques.
Milled
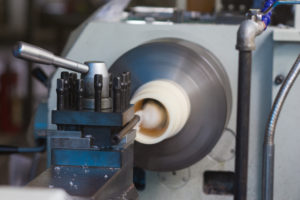
CNC Milling is one of the more common machining options for plastics. This involves using a CNC mill to cut out pockets, change the overall shape and dimensions, and add features to your part.
The problem is that plastic really dislikes heat. If it gets too hot, the plastic can warp, it can melt, or the tool bit can run into problems.
When milling plastic, cutting speeds need to be turned down, and all moves on the machine have to be slower.
Drilled
Drilling entails making holes in your plastic part. This can be done on a CNC mill, or it can be done on a drill press. A drill press is designed to only make holes without any other cuts.
A trained machinist will use the right speed to cut small or large diameter holes into plastic without it shearing or deforming.
With certain plastics like Acrylic, it’s easy to crack the plastic while drilling holes. A trained machinist knows how to avoid this.
Turning
If you put a plastic rod on a CNC lathe, then you can also perform turning operations. Turning is typically an easier process for plastics since it’s easy to keep the part cool and use slower speeds. Turning can change the inner and outer diameters, add holes, or make internal cuts to plastic rods.
Cutting
Cutting is a little tougher on plastics. This entails using a saw, which generates a ton of heat. When rough-cutting plastic on a bandsaw, the machinist needs to be very careful and intentional. Again, a skilled machinist will know how to avoid issues with overheating the plastic.
When to Choose Plastic as a Material
Why might you choose plastic in the first place? In most machine shops, you can choose between different metals, woods, or plastics. In many cases, plastic is the only material that can work.
There are dozens of different plastics to choose from, including nylon, PEEK, and ABS. Each one has unique material properties. In this section, we’ll talk about general use cases of choosing plastic instead of metal.
Low-Cost Parts
In general, plastic is much less expensive than metals. These cost savings add up as you look to make larger pieces.
Of course, there are plenty of exceptions to this rule. High-strength engineered plastics will cost more than metals. However, more general-use plastics can be a fraction of the cost of aluminum bars of the same size.
Amagnetic Situations
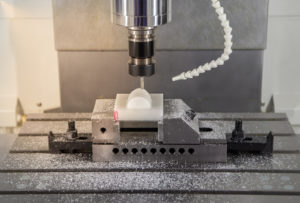
When you’re working around magnets, choosing metal results in an unusable design. Did you know that even aluminum can become magnetized under strong magnetic fields?
Plastic, on the other hand, will never become magnetized. It has to do with the atomic structure of plastic (or polymers, in general) versus metals.
So, if you need to check an airgap on a part that includes a magnet, a plastic shim would be the best option.
Chemical Compatibility
Another great benefit of most plastics is that they are unaffected by a lot of different chemicals. There are hundreds of chemicals that don’t do anything to plastic, but have bad side-effects with metals.
For parts that are used in your process and come in contact with your product, plastic might be the right option.
When Insulation Matters
Most plastics do a great job of insulating electricity, heat, and vibration. If you put a metal piece in the same condition, then it will fail. Again, this goes back to the atomic structure of these two material types.
Weight-Sensitive Operations
Plastics tend to be a lot lighter than metals. For instance, Acrylic is less than half the density of aluminum. If you have loading restrictions or you’re looking to lightweight your assembly, then plastic might be a great option.
The alternative is to cut holes in the metal part to lightweight it, but then you’re sacrificing its strength and wasting time and money in machining efforts.
When Strength Is Non-Critical
One downside of plastic is that it typically can’t handle the same weight as metals. However, it’s a great option when strength isn’t a critical design consideration. For jigs, enclosures, and testing devices, plastic can do a great job.
Machinist Considerations for Plastics
The biggest consideration for machinists when working with plastics is how to manage the heat. Getting a plastic part too hot while machining it can cause the part to get so warped that it’s unusable.
To avoid this issue, expert machinists will adjust their feed speeds, run speeds, and even the cutting bits that they use. They might opt for specialized lubricants to better handle the heat. With enough experience, a good machinist can machine plastic in the same way they would work with a sturdy piece of metal.
Conclusion
As you can see, plastic is a great material to use in a number of different industries. As long as you work with a shop that can handle machining plastic, you’ll have no problems designing plastic parts. For high-quality results, you can reach out to our pros at Rapid Axis. We can handle cutting, drilling, turning, and machining plastic parts.