Metal fabrication is defined as the process of creating and building metal structures from raw metal materials. It involves cutting, shaping, bending, and molding metallic material into the desired final product. Metal-fabrication processes include everything from heavy machinery and equipment to simple hand railings. Specific processes may involve making hand tools, cutlery, structural metals, wires, springs manufacturing, forging, screw and bolt manufacturing, stamping, and architectural metals.Fabrication enables creating an end product from raw materials instead of a product being made from ready-made parts.
Raw materials used in metal fabrications
Before starting a metal-fabrication process, it is necessary to understand which materials are available and determine if they are appropriate for your application. Over the years, the use of common raw materials has resulted in the standardization of fabrication parts and their components. The following outlined raw materials are readily available from a wide range of metal suppliers to suit your fabrication needs.
Casting raw materials
Casting is a process that involves delivering liquid metal into a mold and then allowing for it to cool to harden into the desired shape. Casting is an ideal choice for making products with complex geometries as it has a high degree of flexibility. Molten metal is typically used in the casting process, but concrete, clay, and epoxies can also be used.
The common metals that are used in the process include:
- Iron is a natural chemical element and one of the most common on Earth in its mass. It is plentiful and is an essential material used in the production of steel.
- Aluminum is a lightweight element that is versatile and durable. It also has excellent electrical and thermal conductivity. Aluminum performs poorly at temperatures higher than 400° F, but it is excellent at subzero temperature; hence it is ideal in applications that involve low temperatures like aeronautics or refrigeration.
- Steel is the alloy obtained from carbon and iron. It includes a mixture of iron ore, limestone, coal, and some other elements. It is the most utilized metal in fabrication and has many applications from machinery, construction materials, and even weaponry.
- Stainless steel is an alloy made to have a high corrosion resistant factor. It is composed of aluminum, chromium, carbon steel, and other elements. The metal has a distinctive silver mirror coating. Stainless steel is used in the production of cookware, surgical items, appliances, and cabinet fittings.
- Copper is a tough, malleable and durable metal that is an excellent conductor of electricity. It is highly resistant to corrosion, making it useful for industrial and marine purposes.
- Bronze is a much stronger alloy of copper and is heavier than steel with a lower melting point. It is used in the making of coins, armor, cookware, and weapons.
- Magnesium is a low density and relatively light structural metal. It is ideal to use where stiffness is required over strength. Magnesium is mostly used in aircraft housings, rotating machines, and automobile parts.
- Brass is an alloy produced from zinc and copper. It has acoustic properties making it useful in the casting of musical instruments. It is also used to produce bolts, nuts, doorknobs, pipe fittings, and clock parts.
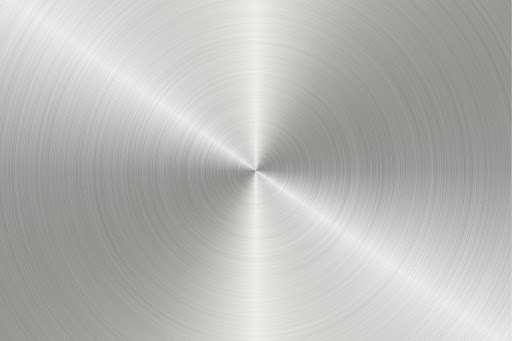
Types of metal-fabrication
- Casting is a fabrication method where molten metal is placed in a mold and cooled to harden into the required shape. Various crafting tools are used to get the desired design.
- Cutting is a fabrication type that involves slicing a metal piece into smaller sections based on the desired size.
- Drawing is a process that involves stretching the metal into a thin shape. Drawing is usually performed at room temperature, but heating can be done if there is a need to reduce the force.
- Folding is manipulating metal to make it bend at a specific angle. It is mainly done using a brake press that pinches the metal to make creases. It can also be done by a folding machine or by hammering the metal piece manually until it bends.
- Forging is where compressive force is used in the shaping of metal. A hammer hits the metal piece until the required shape is formed.
- Extrusion is the process that is used to roll a metal sheet into a cylindrical shape to form a wiring or piping structure.
- Machining is the removal of unwanted material from a metal piece to shape it. Machining can be done through milling or drilling.
- Punching is the creation of holes through a metal piece using a punch press.
- Shearing is the process needed to achieve long straight cuts on metal. It involves using two tools; the blade on the upper part and a stationary lower blade that applies pressure on the metal.
- Stamping is a process that is similar to punching, except an indentation is placed rather than a hole. It is used to form letters, images, or shapes on a metal sheet. For stamping, crafting tools or a press can be used.
- Welding is a process that involves combining two or more metal pieces using heat and pressure.
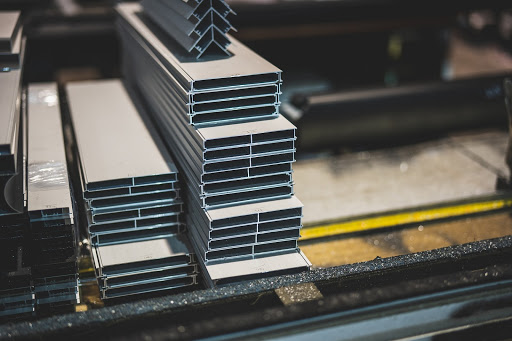
Sectional metals
Sectional metals are made of steel and are available in standardized sizes and shapes. They are mainly for construction and engineering purposes. Different types of sectional metals’ chemical and physical properties have already predefined standards. The common types include:
- I-beam is a long steel beam with a cross-section that looks like the letter ‘I.’ Both flanges of the beam have a slope on the inner surface that is generally 1:6 making the flanges to be thick inside and thin outside. The H- beam and Wide Flange (WF) beam are varieties of this beam category.
- Z- shape is a beam that resembles the letter ‘Z’ and has a half flange that protrudes in the opposite direction.
- Hollow structural section (HSS) is a type of steel beam that has a hollow cross-section. They are made in various standard shapes, i.e., circular, square, elliptical, or rectangular cross-sections.
- Bar is a type of sectional metal with a rectangular cross-section that is long and flat.
- Rod is a piece of sectional metal that is long and is square or circular in nature.
Flat metals
This is metal that has been rolled and pressed to form thin flat pieces. The flat metal thickness is measured in gauges and may vary from several centimeters to lower than a millimeter. Flat metal raw materials can be classified into three categories:
- Sheet metal is the most common type, with a thickness of six millimeters in size.
- Foil or leaf metal is paper thin, and is in fact the thinnest of the flat metals.
- Plate metal is the category of any flat metal that has a thickness above 0.25 inches.
Welding-wire
Welding-wires are composed of easily soldered metals formed into circular rods. They are used in the welding process, where they bind two or more metal pieces together. Welding wires are ignited to render the wire soft and create a heated arc to join metal pieces. They are made in a wide range of sizes and metal materials to allow customization in welding.
Formed and expanded metal
Expanded metal is formed from steel sheets, simultaneously expanded and slit in cold conditions to create diamond-shaped openings of uniform thickness and size. These holes are surrounded by metal strands that are interlinked to expand to the final size. The resulting grate-like sheets are used for outdoor furniture, screen doors, fencing, and other architectural designs. They are also used in industries as guard rails to avoid direct contact with the hot machinery.
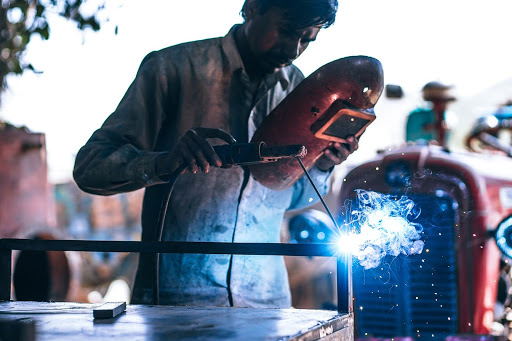
Hardware
Hardware is defined as the different parts or fittings used to make a particular product stronger and easier to fabricate. They include materials such as:
- Corners are angle cut metal pieces that are used to join metal pieces at a 90° angle.
- Handles are used to provide easier holding of a metal plate.
- Locks are a mechanism placed on a metallic structure to lock two or more pieces in place.
- Keys come hand in hand with locks to provide an opening mechanism.
- Chains are used to tie together or suspend metal pieces.
Tools used in metal-fabrication
- Band saw is a power saw with a sharp, long blade consisting of a metal band that is toothed and stretched on two or more wheels for the cutting of objects. It is ideal for making a uniform, irregular or curved cut on a variety of materials.
- Bench shears are used to cut rough shapes from metal sheets. The only disadvantage is that they cannot perform delicate cuts.
- Power shears are used to cut metal sheets more quickly and with limited manual effort. They are not able to cut tight corners or intricate shapes.
- Tin snips are hand-operated shears that resemble scissors with thick handles and short, strong, sharp blades used to cut thin gauge sheets of metal like stainless steel.
- Chisels are cutting tools with a sharpened wedge at the bottom, often used with a mallet or hammer to cut or shape metal. A chisel is regarded as part of the crafting tools.
- Grinders are tools that are used to process material by grinding or crushing them into smaller pieces. Grinders are also used in polishing metal surfaces.
- Cleco fasteners are a set of tools that temporarily hold multiple metal sheets together before joining permanently or drilled.
- Grinder discs are made of coarse, rough material bonded together to form a circular shape. These wheels are used in grinding machines.
- Wire cutters are special pliers that are designed to cut wires using their jaws.
- Glass cutters are used to make a shallow intrusion on a glass surface that needs to be broken. The glass breaks along the scoring that was made depending on the shape introduced.
- Hobbing machines are machines that are used for cutting gears, sprockets, and splines.
- Milling machines are used to remove layers of material in groove forms from a metal piece’s surface using a multi-point cutter.
- Honing machines are used to improve the form of a particular surface by producing a precision surface on the metal piece through scrubbing with a grinding wheel in a controlled path.
- Planers are machines used to produce accurate cutting slots and flat surfaces.
A summary on metal-fabrication
This guide has explained a lot about the raw materials used in metal fabrication, and hopefully you have a better understanding of the way it works.. Metal fabrication has a very broad application in many industries and also in consumer products. Nowadays, most companies have adopted advanced machinery to increase the rate of work being done. Metal fabrications experts are therefore needed to create such equipment.