Intro
There are a lot of ways to make a sheet metal piece very expensive. The worst part is that you might not even realize you’re making one of these common mistakes until you get a crazy-high quote from a manufacturer. Our machinists put together this list of 7 ways to reduce your sheet metal manufacturing costs — take a look.
Remember the Optimal Bending Radius
Bending is one of the key sheet metal fabrication methods, and it seems like an easy enough thing to do if you’ve never seen it done. Well, sheet metal is pretty picky about how it likes to be bent.
More importantly, machine shops are restricted when it comes to certain bends.
The truth is that you’ll never get a bent piece of sheet metal that’s 90-degrees and has a square corner, there’s always a radius. The rule of thumb is to design for an interior bending radius that’s equal to the thickness of the sheet, at least.
For example, bending a 10-gauge sheet of aluminum (which is 0.102” thick) would require a minimum internal bending radius of 0.102”.
Choose the Right Base Material
As alluring as titanium and specialty materials are, they’re the quickest way to increase your manufacturing costs. Not only is the base material more expensive, but all subsequent manufacturing processes are more expensive as well.
We suggest sticking with common metals like 6061 aluminum, 304 stainless steel, and a low-carbon mild steel like CRS1008.
If the part is going in a rough environment, you can opt for a pre-plated material as long as you don’t require any welding. Otherwise, you’ll need to plan for plating, anodizing, or powder coating the part after fabrication.
Forget Unnecessary Design Elements
It’s easy to overdesign a part when it’s sitting on your computer screen. The best practice is to design your part with manufacturing in mind at all times.
This might mean removing features that were included strictly for aesthetics. Something that can be done with one click on your screen (like fileting or sweeping a component) can take hours in the shop and amount to a lot of added money.
After fully designing a piece, try to go over the design with a machinist if you can. Ask them to pinpoint areas that would be difficult to fabricate, then ask yourself if the associated design elements are mission-critical.
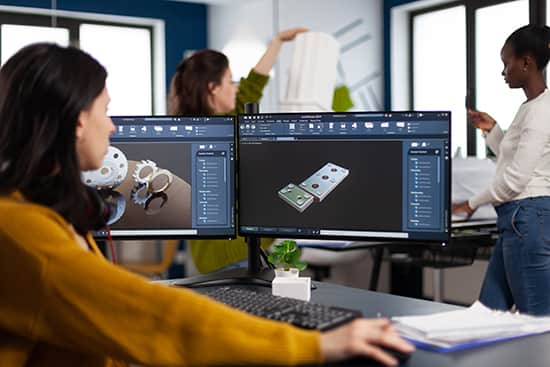
Keep the Drawing it Simple and Clean (for the Machinist)
Another way to reduce the final cost of manufacturing is to keep all of your drawing packages clean and simple. Anything that could add confusion should be omitted.
Sometimes, this means creating multiple drawing packages for your different third-party manufacturers. Yes, this means added efforts upfront, but it can save you a lot of money in the long run.
For instance, your fabricator doesn’t need to get an assembly drawing if they aren’t doing any assembly. It might leave them scratching their head and then giving you a call before moving on.
The same is true for added drawing notes. Sometimes it’s helpful to have notes off to the side, but the truth is that your three-view and iso should tell the full story.
A joke in some manufacturing plants is that “technical drawings are a universal language” since they should include no written language — just a series of dimensions, tolerances, and easy-to-understand views.
Cheap Fasteners are King
You’d be surprised to see how many designs we receive that include high-tech (and expensive) fasteners in an application where a cheap fastener would work just as well. Any typical machine shop has shelves filled with common fasteners.
If you call out a specialty fastener, then there’s a good chance the shop will have to special-order the fastener. This adds money and time to your project. Whenever you can get away with using cheap fasteners, you should.
Simplify the Design
The simplest design is typically the least expensive to make. If a designer spends an extra week on a design just simplifying it, they can easily halve the final cost of production.
Every feature in a design equates to dollar signs. The more a machinist needs to do, the more expensive the part will be for you.
With experience, the idea of simplifying designs starts to come naturally.
Use Off-The-Shelf Options Whenever Possible
Do you really need a bent piece of sheet metal, or can you use angle iron? Questions like this can save you a lot of money on sheet metal manufacturing.
Off-the-shelf options are much less expensive and quicker to get than custom-made sheet metal pieces.
We always implore designers to shop through catalogs like McMaster-Carr’s before starting a sheet metal design. You never know, you could find exactly what you’re looking for in a product brochure.
If nothing else, you can use these off-the-shelf components in junction with your design. Instead of bending a flange, you can include angle iron that gets fastened to your sheet metal body.
Conclusion
By following our 7 tips, you should get much lower quotes to manufacture your parts. If you want to talk through some of these ideas and see how they pertain to your part, reach out to our pros at Rapid Axis. We can take care of your sheet metal fabrication needs and give you high-quality parts.