Intro
When it comes to designing a part for manufacturing, there’s a lot to consider. It’s something that takes a lot of practice before you can get really good at it. To speed up your path to perfection, our machinist put together this quick guide.
We’ll review 4 common mistakes to avoid when designing for manufacturing. We’ll discuss why these mistakes are critical, and how you can save money and time by avoiding them.
What Is Design for Manufacturing (DFM)?
There’s a concept in engineering and design work called “designing for manufacturing”, or DFM. The theory is that you should make the part easy to be manufactured. Why? It can save you time, avoid a lot of phone calls, avoid miscommunication during manufacturing, and save you money on every part.
If you make a part that looks nice on your 3D CAD software but a machinist can’t make it, your project is a non-starter. This is why engineers will spend a lot of extra time during the design phase to make their parts manufacturable.
When a part uses DFM best practices, the machine shop can finish the part quickly without any confusion and send it right to you. If not, there can be some hiccups along the way that can hurt your timeline and budget.
4 Common Mistakes to Avoid When Designing for Manufacturing
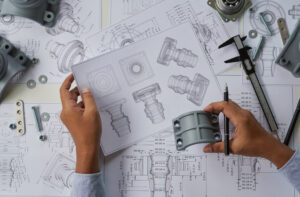
Without further ado, here are the 4 most common mistakes that designers should avoid when they’re designing for manufacturing.
Not Knowing Machine Capabilities
First and foremost, you need to know what the machines can physically do. We always suggest that engineers and designers do a rotation in a machine shop, to get some invaluable hands-on experience.
We’ve seen plenty of designs that are beautiful on paper and probably work perfectly in the designer’s application, but they’re nearly impossible to machine.
Here’s a quick example: making a perfectly square pocket in a part. CNC milling machines use circular bits, so you’ll always get a radius by default (even if the mill goes in a square pattern).
If you didn’t know this, then you might design a part that specifies 90° corners in a pocket. When the machinist sees this, they’ll have to reach out to you to fix the problem. It requires some extra design or specialty tooling to do. That means time and money are wasted at a critical point.
In general, it’s best to know what the machine can handle before you design the part. Try to imagine how you would machine the part, personally. That way there is no confusion or issues when the machinist gets to work.
Requiring Machining That’s Too Difficult
Another common mistake that we see is an engineer who creates a part that is intentionally difficult to make. There might be a good reason to design your part a certain way, but you should always think through ways to simplify the manufacturing.
For one-off parts, it might make sense to call for difficult features. But, if you’re making a number of parts, the added efforts really pile up and can result in a lot more money and time wasted.
An example of intentional machining that’s too difficult is a part that requires multiple setups on the machine to make. This could look like threaded holes going at random angles, and odd cuts and features that aren’t orthogonal to the six design planes.
Ultimately, it’s a trade-off. Do you want to make the design work easier, or the machining easier? We suggest leaning towards the latter.
Forgetting Details and Specifications
Putting together a complete drawing package is an artform, and it typically takes a lot of practice. Knowing which views to include, when to put detailed or section views, and how to call out the features isn’t easy.
At the end of the day, we know that it’s easy to make a mistake and forget details or specs on your drawings (we’re never going to get mad about this). But, you should spend some time reviewing before sending out your drawings.
Sit down with another engineer to peer-review your drawing. Check for forgotten details or specs.
Even if you forget just one length dimension, there’s a chance that the part will be impossible to make. We’ll need to contact you to get the missing dimension.
If you don’t have a spec for surface finish, roughness values, or added finishing steps, they’ll likely not get done. You’ll receive a part you don’t want thanks to drawings that weren’t complete. After all, the machinist can’t assume what you might want.
We always say, “a dollar on the drafting table can save you ten dollars in the shop”. Double and triple-checking your drawing can help you avoid getting parts you can’t use, having conversations about missing details, and wasting time during the manufacturing process.
More detail is usually better. Adding redundant dimensions isn’t the end of the world, and putting an isometric view on the sheet is always a good idea.
Using Non-Standard Materials, Sizing, or Components
Manufacturing experts love the idea of “standard”. Standard materials, sizing, bits, components, parts, and finishes make everyone’s lives easier.
A standard part is one you can grab from Lowe’s today, and a standard material size comes from our metal supplier already done. If you design a part that needs to be 12” long plus or minus a quarter inch, we can skip any rough cuts or machining to bring a 12” long piece down to size.
If you need a non-standard part size or hole, that’s one thing. If it can’t be avoided, then there’s no problem. The problem arises when the designer calls for a non-standard size when they don’t actually need one.
For instance, making a 0.250” diameter hole is easy. We can grab an E-size drill and finish the hole in a minute. Making a 0.2545” diameter hole? That’s going to require boring and a CNC machine to custom-make the part since there’s no drill bit for that size.
This is a good example of what we mean by non-standard sizing. Always stick with nominal dimensions and sizes whenever you can.
Conclusion
Avoiding these 4 common DFM mistakes can save you time and money and avoid unneeded headaches. Remember these mistakes moving forward and try to avoid them in every design you send for fabrication. If you want a trusted manufacturing partner, consider our team at Rapid Axis. We’re a full-service machine shop and we can handle your projects (even if you made some of these mistakes). Contact us today for a free quote.